When the Stainless Steel & Special Alloys Committee of the Brussels-based Bureau of International Recycling (BIR) met in Shanghai in late May 2013, prosperity and optimism were not part of the prevailing mood.
Several traders who sit on the committee and guest speaker Markus Moll of Austria-based Steel & Metals Market Research referred to reduced generation of and demand for stainless steel scrap as prevailing concerns in 2013.
Although some presenters also referred to factors that are likely to breathe new life into the stainless and specialty alloys sectors at some point in the future, the summer of 2013 has largely been more of the same for this downtrodden segment of the industry.
Something Special
A healthy aerospace industry is a source of good news, at least for traders involved in the high-temp and special alloys sectors.
Phil Rosenberg of Keywell LLC, Chicago, noted that “the relaunch of the Boeing 787 is a good sign for the marketplace” and that Airbus also has announced new orders. For the past several months, the aircraft alloys metal supply chain had “backed up,” Rosenberg said, as aircraft production slowed down.
Several aircraft orders had recently been announced when Rosenberg made his comment in late May, and several additional aircraft orders have been announced by manufacturers during the summer of 2013:
- Sky West in the U.S. placed an order worth up to $8.3 billion for from 100 to 200 regional jets from Brazil’s Embraer;
- TUI Travel, a United Kingdom-based firm that operates six airlines, placed an order for 60 Boeing 737 aircraft from the U.S.-based plane manufacturer;
- Singapore Airlines split its $17 billion order between Boeing and Airbus, including 30 787 Dreamliner models from Boeing;
- Canada’s Bombardier confirmed an order for 10 of its aircraft by Bahrain’s Gulf Air that was first announced in 2011;
- Beechcraft Corp., Wichita, Kan., said in early August that it had received an order for up to 105 propeller planes (valued at $788 million) from Wheels Up, New York, a private membership-based aviation provider;
- The U.S. Navy signed a nearly $2 billion contract with Boeing in early August to purchase 13 Poseidon patrol aircraft;
- Brazil’s Embraer announced in mid-July that a Los Angeles-based leasing company had agreed to purchase 50 jet aircraft from it for $2.85 billion;
- In mid-May, Boeing confirmed an order for 50 737 planes from Turkish Airlines, while Kuwait Airways was considering placing an order for 25 aircraft from Airbus; and
- Airbus said it had received 446 orders as a result of the Paris Air Show and by July reported a total of 932 planes ordered in the first seven months of 2013. That was up from a previous estimate of 700 to 800 planes ordered.
In terms of military spending, India took delivery in mid-2013 of the first of eight reconnaissance planes from Boeing. India has spread its military aircraft spending among multiple nations and manufacturers, also having ordered transport aircraft from Lockheed-Martin of the U.S. and up to 126 fighter aircraft from Dassault Aviation of France. India also may buy as many as 37 military helicopters from divisions of Boeing.
More Down to Earth
While the aerospace sector offers promises of future activity for specialty alloys traders, the larger volume stainless steel scrap market remains in the doldrums.
“The demand both domestically and offshore remains very weak with no real improvement in sight,” says James Lawrence of ISA Alloys, Louisville, Ky. “For the scrap recycling community, orders remain low and will continue to be so until that demand begins to pick up. The future for 2013 is not very bright and this could continue into mid-2014.”
Lawrence’s midsummer comments provide an update to remarks made at the BIR meeting in late May by Barry Hunter of Hunter Alloys LLC.
Hunter said the North American Stainless mill in Kentucky “remains the volume scrap buyer” in the U.S. and the new Outokumpu mill in Alabama (recently acquired from ThyssenKrupp) “is currently running on a limited production basis [and] it has really no influence on the current scrap [U.S.] market.”
Lawrence says he observed the same pattern during the summer relative to the new Outokumpu mill, which continued to downsize its forecast in light of low demand. “It appears that they remain in startup mode and most likely will remain that way until sometime in 2014. Their buying has lessened considerably since March,” Lawrence observes.
Demand from export markets has not stepped in to fill the breach, with China’s hunger for stainless scrap falling well below its appetite for copper or aluminum. China is able to provide much of its own feedstock to make stainless steel by producing nickel pig iron domestically.
“Demand has remained flat to down pretty much everywhere, and there has been an equivalent pricing adjustment in relation to the London Metal Exchange (LME) basis on which nickel in scrap is valued,” says one stainless scrap export broker.
“The offshore situation is not much better,” agrees Lawrence. “Nickel pig iron is going to remain a factor in the years to come, especially in Asia where it is produced and because China is the major user of nickel. Currently it seems that they continue to produce, and this continues to add to the surplus of nickel. This continued production and continued increasing of the nickel surplus is having a major impact on the price of nickel.”
The lack of demand has been somewhat balanced by a lack of supply, Lawrence says. Low LME nickel and stainless scrap prices have caused a “wait and see” attitude, he says, resulting in generators and smaller dealers holding onto stainless material waiting for better prices. “This holding of materials is causing a false shortage or tightness in supply in the hopes of these higher prices,” he comments.
Lawrence also says that U.S. manufacturing was not producing large amounts of scrap and that he was skeptical about the construction rebound.
Europeans who spoke at the BIR event said they did not foresee greater stainless steel production figures or scrap demand as being likely in Europe anytime soon. “2013 seems to be another year of challenges,” said Ian Hetherington of the British Metals Recycling Association.
Guest speaker Moll backed up Hetherington by saying the European stainless industry “is on its knees at the moment” with most of its producers unprofitable.
He also noted that stainless scrap processors in Europe are not helped by the fact that 83 percent of stainless scrap is consumed on the continent it is generated.
China’s energy woes will make it increasingly expensive to smelt its own nickel pig iron. Imported stainless scrap may become competitive again by 2015.
If that happens, it could change the relatively static nature of stainless scrap flows.
Substitution Patterns
A trend in the stainless steel industry for several years has been a switch by finished product manufacturers to using low-nickel content 400 series stainless grades rather than higher-nickel 300 series alloys.
Moll told BIR delegates that the ability for manufacturers to substitute these lower-nickel-content alloys for high grades of stainless may have nearly reached its peak.
High-grade 300-series stainless alloys made up 80 percent of the market in the late 1980s, noted Moll. That figure dropped to the 65 percent range by 2005 and continues to fall, currently residing at 56 or 57 percent.
Moll, however, said he did not see the 300-series market share falling below 54 or 55 percent, hitting this floor in 2016 or 2017 and “stagnating” there. Moll also identified seven “mega-trends” and shared his observations as to how they affect the stainless steel industry:
- Demographic changes will continue to bring growing wealth and urbanization to emerging countries.
- The demand for more and efficient energy may mean smaller engines but more stainless components used in biofuel applications.
- Resource scarcity could trigger ongoing volatile pricing and the search for alternative materials.
- Changing design principals could favor stainless steel, but longer life cycles could portend longer waiting periods for stainless components to become available scrap.
On the demographic side, the differences are already apparent looking at Moll’s 2010 to 2013 figures and forecasts for regional stainless steel growth.
China will add 860,000 tons of stainless output in 2013 compared with the year before, more than half of the world’s total of 1.23 million tons. The rest of Asia is the next biggest contributor to global stainless output, adding 190,000 tons in 2013.
Who's Doing the Melting? To demonstrate that the balance of stainless steelmaking power has shifted to Asia, one can look at national production figures or at the roster of the world’s largest stainless steel companies. A chart created by Steel & Metals Market Research (SMR), Austria, and its Managing Director Markus Moll to demonstrate industry consolidation also demonstrates its now Asia-centric status. Based on 2012 figures, each of the four largest stainless steel producers are now Asia-based:
|
North America, meanwhile, will add just 80,000 tons of output, if Moll’s forecast is correct, while Europe will produce 80,000 fewer tons in 2013. The rest of the world, however, contributes to the 1.2 million tons of stainless steel growth.
“We believe some melt shop closures in Europe are unavoidable,” said Moll. “I’m convinced we need melt shop closures in North America also,” he added, noting that the new Outokumpu mill in the U.S. will create considerable new capacity there.
With stainless production growing in China and Asia, processors and traders in North America may soon become more familiar dealing at longer distances. “Asia needs to generate 7.6 million metric tons of scrap by 2020,” Moll said. He predicted such generation was unlikely, adding that the continent’s producers may need to import some 2.8 million tons of stainless scrap from North America and Europe.
The author is editor of Recycling Today and can be contacted at btaylor@gie.net.
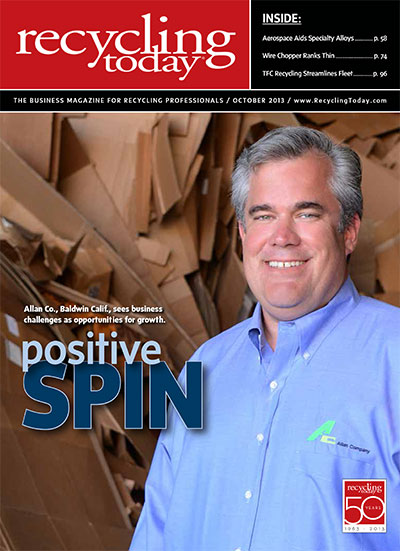
Explore the October 2013 Issue
Check out more from this issue and find you next story to read.
Latest from Recycling Today
- Waste Robotics and Greyparrot form partnership
- FEAD publishes manifesto calling for European circular material use act
- Report: Suzano preparing $15B bid for International Paper
- Cascades reports net loss in Q1; CEO says results met expectations
- Plastics Recycling Show Europe announces conference program
- Delos and Silverfern Group complete sale of Pioneer Recycling Services
- Simplified Environmental Solutions adds 2 locations
- Glass Recycling Foundation awards $150K in grants