Something old; something new; something borrowed; something blue. This traditional bride-to-be rhyme could easily apply to the recycling industry which uses old and new sorting technologies; has borrowed some technologies from other industries; and uses blue bins and bags in many cases to designate recyclables. Together, all four areas combine to make the sorting of various recyclables a productive process, but it’s the “new” and “borrowed” technologies that are of particular interest to processors as they look for ways to become more productive and profitable.
Although it is not possible to focus on every minor advance in sorting technology, processes to sort mixed broken glass, paper from cardboard, and the multiple grades of plastics are of particular interest because of the challenges these areas present.
SORTING BROKEN GLASS
Several new glass sorting systems have appeared in the United States recycling market – but they aren’t actually new at all. One company, Countec Recycling Systems, Des Moines, Iowa, recently introduced into the U.S. a proven glass cullet sorting system from Europe. The system, made by SEA International, Villanova, Italy, was originally used in the food processing industry to sort different grains of rice, coffee beans and other foods. Then, several years ago, the technology was adapted for the glass recycling industry and units began appearing at glass manufacturing plants throughout Europe.
The SEA 160V sorting machine is capable of a binary sort of glass cullet by using 64 optical sensors and directed blasts of air to identify and remove targeted materials such as ceramics, metals or colored cullet.
Another European company, S+S Metallsuchgerate in Germany has a similar system that is being marketed by Carpco Inc., Jacksonville, Fla. The S+S device, called the JAG 8100, separates the cullet by color using mixed-color lasers and filters for identification and air blasts for particle removal. The machine also avoids false separations caused by dirt or paper labels because the laser measures the wavelength in the colored glass. Carpco has just started marketing the system in the U.S.
The JAG 8100 can be combined with Carpco’s MALAG 1024/4 detector/separator that uses magnetics and multi-channel lasers to detect metals and non-transparent impurities (such as ceramics). The impurities are removed with pinpoint blasts of air.
Yet another new cullet separation machine made by Binder of Austria is also available on the market, and Magnetic Separation Systems, Nashville, has introduced its third generation glass sorter called ELKE that has an upgraded detection array sensing system.
“The driving force for these types of machines in Europe has been the glass industry,” says Richard White, director of sales and marketing for Countec. “They have taken the lead in this area because the glass manufacturers want quality post-consumer cullet. Over there, a typical bottle has about 90 percent recyclable content. One plant, for instance, has 13 of these glass sorting machines doing various sorts.”
The SEA 160V should pay for itself in about a year, according to White. “If a MRF is receiving about 1 to 3 tons of mixed broken glass an hour, then the payback can happen fairly quickly.”
SUPERSONIC SEPARATION |
If the recent movie “Twister” has you feeling just a little helpless and terrified of the vile vortexes, then think of what it would be like as a piece of composite plastic inside an Ultrasonic Vortex Generator as you spin faster than the speed of sound. The new ultrasonic separation system, which is made by the Swiss company Result AG and marketed in the United States by Result North America (formerly HGI), Asheville, N.C., uses the super high-speed USVG to accomplish two steps. First, it neutralizes the material bonds and adhesive forces that hold the different types of particles together. Thus, plastic is liberated from metal, and so on. Second, it turns plastic particles into flakes and metals into small spheres. Once this happens, the materials can be separated according to their densities. The complete system employs other pieces of equipment such as a pre-shredder, metal separator, screw conveyors, shaker tables and air knives all connected by various types of conveyors. According to Jerry Hoffmann, vice president of Result N.A., the system allows a very efficient separation and classification of materials with purity levels of up to 99 percent. Hoffmann claims that the system can effectively recycle all types of composites and laminates including fine plastic-coated wires, automotive dashboards and trim items such as chromed plastics and bumpers. Even automotive shredder residue can be separated, says Hoffmann, along with computer circuit boards and other computer and electronic waste material. “The advantage to this system is that it does not employ heat or chemicals,” says Hoffmann. “It takes place under ambient conditions, so there are no toxic vapors or other harmful substances emitted.” |
BORROWED FROM MINING
More borrowed technology for recycling comes from the mining industry. Deister Concentrator Co., Fort Wayne, Ind., has been making its concentrating tables for mining operations since 1906, but it was only last year that the company began to truly target the recycling industry. The technology was first used to recover particles of gold from soil.
The tables work in tandem with special cyclones to recover targeted materials from chopped, flaked or fine waste streams that contain numerous types of materials. By immersing the material stream in water, the system can sort out a target material by concentrating on that material’s specific gravity in relation to water and the specific gravities of the other materials. Thus, those particles with the same specific gravity concentrate together and can be effectively separated and removed.
Deister is currently targeting wire chopping operations, shredder fluff and material streams from computer and integrated chip recovery operations. The company will accept samples of material streams and conduct separation tests for free at its Fort Wayne headquarters.
“From the last show we were at we received about 50 samples of various material streams for testing,” says Nick Griffith, president of Deister. “So, we are just beginning to see what we can do.”
Giffith says that the company is going another step further toward enhancing and customizing its system for the recycling industry by developing add-ons that will make the tables and cyclones part of a new closed-loop recycling system. “Basically, all you will have to do is push a button and stand back,” says Griffith.
In addition, the company is working on building a prototype site somewhere in the South that will be a working recycling operation. “It will allow us to better demonstrate our capabilities,” adds Griffith.
Another company that has transitioned mining technology over to the recycling industry is Carpco. “It really is a natural fit because of the commonalities between separating mineral particles and recyclable commodities,” says Julie Holloway of Carpco. “In both industries the natural properties of the material are being examined and evaluated – is it conductive or not, is it heavy or light – so that it can be separated.”
Carpco has a new processor, just commissioned at press time, that targets chopped wire. The new system, designated AFS, is a three-stage machine that uses dispersion, flotation and screening to separate the metal from the plastic without contaminating the end products.
In another crossover area, General Kinematics, Barrington, Ill., developed its De-Stoner first for cleaning up sawdust from lumber mills, then found that, with slight modifications, the machine could be used in the recycling industry. The De-Stoner is currently being used to sort commingled streams based on density and particle size using vibrating and air fluidizing sections.
SPECIAL SCREENS
In the fiber processing area, special screens have been adopted or developed to effectively sort old corrugated cardboard from paper. Van Dyk Baler Corp., Stamford, Conn., has adapted a sorting screen called Starscreen that is made by Lubo Equipment in the Netherlands. The screen was originally designed for the composting and construction and demolition debris recycling industries about 18 years ago, but was crossed over to the fiber recycling arena only recently. It uses rubber star-shaped disks that rotate in a pre-configured series. The fingers of the stars bounce the OCC over the screen, and grab the paper downward through the rotating disks.
According to Erik van Dijk, vice president of Van Dyk Baler, the screen can also sort commingled containers, separating whole bottles and cans from broken ones and other contaminants, or it can sort a fiber mix with occasional non-fiber contaminants.
Another new OCC/paper screening system is made by Bulk Handling Systems Inc., Eugene, Ore., and it also uses specially-shaped disks. The sorter has been on the market for just more than a year.
The machine sorts OCC and paper by using a unique, patented screen called a Debris Roll Screen. The screen is made up of non-circular, in-line disks that, through their rotation, create an agitation. The action throws OCC forward and lets paper drop down. The company currently has three models up to a 25-ton-per-hour capacity.
“The system can also be used for commingled streams, where there may be broken glass or other contaminants in the fiber stream,” says Sean Austin, sales and marketing manager for Bulk Handling Systems.
Austin also says that the disks in his separator can be made of rubber or steel, but the rubber is becoming more popular because it grabs the OCC better when throwing it.
A FASTER PLASTIC SORT
In the plastic bottle sorting arena, Magnetic Separation Systems has recently developed a follow-on generation sorter that has a higher throughput than previous systems. It’s called the Binary BottleSort System.
This new system just went on the market, and it differs from the original BottleSort machine that was introduced in 1991 in two major ways. First, the Binary system only sorts out one target resin at a time, whereas the original BottleSort sorts multiple resins at once. Secondly, the Binary system has a much higher throughput because it looks at the bottles across a single layer (called a non-singulating process), whereas the other system examines each bottle individually (a singulating process).
“In the original BottleSort, each bottle was examined as it came down the line,” says Derek Vaughan, marketing director of Magnetic Separation Systems. “But in the Binary system, the bottles are laid across in a single layer and the detecting array looks at the grouping as it passes by. If it finds a bottle that is not the target resin, then a jet of air above the layer blows it out. Because of this method, and because the machine is only targeting one type of resin, the throughput can be up to 5,000 pounds per hour per line depending on the model chosen, as compared to only 1,250 pounds per hour for the original BottleSort. Plus, the Binary machine is only about 20 feet long, compared to 60 feet for the original BottleSort system.”
Depending on the desired sortation, the Binary system can be aligned in series to conduct multiple sorts like the original BottleSort.
National Recovery Technologies Inc., Nashville, is working on a laser-based plastic sorting system using a detection array that would also be non-singulating and would kick out targeted resin types via an air blast or other method. “The system can be used for all forms of plastic streams, and not just bottles,” says Guy Wentworth, vice president of NRT. “We already have a working model, and we just need to add the ejection method.”
Last year, NRT introduced its non-singulating MultiSort plastic sorting system that uses optics to sort bottles by color or resin.
One plastic sorting area that has had little development is in the sorting of rigid resin containers, such as butter tubs. But according to Peter Dinger, director of technology for the American Plastics Council, Washington, research is currently progressing in this area.
“We are working with a company to sort out tub resins by using size characteristics,” he says. “The system is a singulating sorting system,” says Dinger, “and we are trying to run the lower profile plastic tubs through and identify them due to their size then kick them out of the stream. The biggest concern right now is processing throughput efficiency.”
Others in the industry look to special identification codes that could be integrated into the plastic packaging itself, making resin recognition and mechanical sorting easier.
The drive to make the sorting process more cost-efficient, combined with advances in computer-processing technology, will likely shape the way recyclables are sorted in the future.
Because of the cyclical nature of the recycling business, prices for materials fluctuate drastically. Thus, those who can sort materials more economically will have an advantage.
Helping recyclers achieve that goal will be a dramatic leap in computer processing and miniaturization.
“We are heading toward a time in the plastic sorting segment, for example, when the technology will allow companies to reduce the number of steps it takes to process material,” says Vaughan. “The computer processing and storage technology is moving so fast that soon the same amount of information that is now stored on a compact disk will be stored on a disk the size of a penny.”
Vaughan says that these advances will allow developers of sorting equipment to design machines that can conduct more complicated sorts faster. Plus, the technology will allow the machines to remain affordable.
The author is managing editor of Recycling Today.
ROBOTIC SORTING |
National Recovery Technologies, Nashville, Tenn., recently received a U.S. Dept. of Energy grant of more than $700,000 to develop a system that would sort commingled recyclable streams using robotics. The sorting method involves robotic arms or devices on a picking line that would replace manual labor. Under this system, a programmer would view the incoming waste stream via a console and initiate signals to the robotics to remove items off the line. The company has two years to develop the system under DOE guidelines. “We have already demonstrated that this could work while maintaining the same throughput of a manual handpicking line,” says Guy Wentworth, vice president of NRT, “but with reduced labor costs.” |
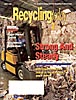
Explore the July 1996 Issue
Check out more from this issue and find you next story to read.
Latest from Recycling Today
- Waste Robotics and Greyparrot form partnership
- FEAD publishes manifesto calling for European circular material use act
- Report: Suzano preparing $15B bid for International Paper
- Cascades reports net loss in Q1; CEO says results met expectations
- Plastics Recycling Show Europe announces conference program
- Delos and Silverfern Group complete sale of Pioneer Recycling Services
- Simplified Environmental Solutions adds 2 locations
- Glass Recycling Foundation awards $150K in grants