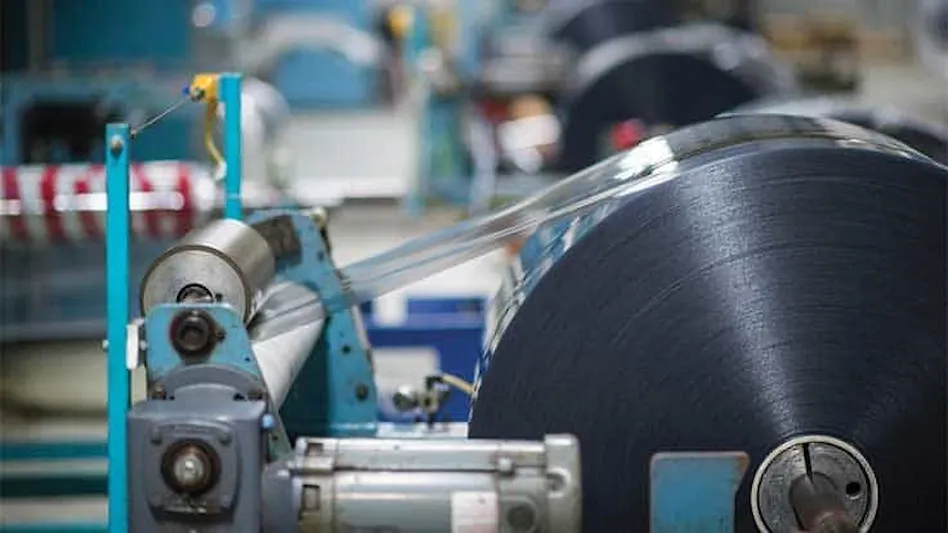
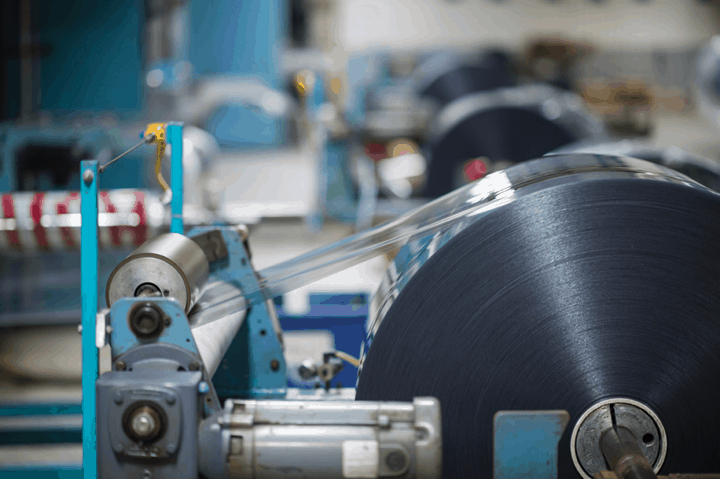
Some companies are beginning to think about their place in the circular economy, but Wisconsin packaging manufacturer Placon already knows where it stands. It has been producing thermoformed packaging with postconsumer content for the past 29 years and recycling bales of polyethylene terephthalate (PET) bottles in-house since 2011.
“In the sustainability arena, there are a lot of people making a lot of claims,” says Placon Chairman and CEO Dan Mohs. “We have been out there innovating in the sustainability space since before people even knew what sustainability meant.”
Innovating packaging
Placon is a major North American manufacturer of thermoformed clamshells, trays and blister packaging with a long pedigree in engineering innovative packaging. It has about 30 designers and design engineers on staff.
The company’s strong commitment to sustainability is unique. It has made a substantial, long-term investment that enables it to buy bales of postconsumer PET bottles and thermoforms and turn them into new thermoformed packaging. The recycled flakes and rollstock it produces are trademarked EcoStar.
Currently, Placon produces 22 million to 25 million pounds of recycled flake per year and uses it to make rollstock for in-house production. The recycled flake goes into about 80 percent of all the packaging Placon produces, which is primarily used in food and retail applications. About 60 percent of the company’s products are custom, while the remaining 40 percent are stock items.
Tom Mohs, Dan’s late father, started Placon in 1966 with a thermoforming machine he built in his basement to make plastic jewelry boxes. Today, the privately owned company has more than 750 employees with facilities in Wisconsin, Minnesota, Indiana and Massachusetts. It has annual sales of more than $200 million.
Placon has more than 30 U.S. patents and continues to be a leader in the thermoforming industry.
Placon had early success when Tom designed and patented a small retail package to hang on a pegboard and hold fasteners. He started with his jewelry box design and added a living hinge. This was the first clamshell container, and he trademarked the name BlisterBox.

Another milestone came in 1991 when Placon developed the first recycled PET retail package in the United States, which was introduced at Walmart stores.
“Walmart initiated its first green program around packaging in the early 1990s, and our customers were trying to respond to that,” Dan says. “There were a lot of companies experimenting with different things like polystyrene solutions, but we decided we were going to try to use postconsumer recycled PET bottles and thermoforms.”
Placon initially purchased recycled PET sheet from Wellman Plastics Recycling to manufacture the packaging.
“We used to make all those clamshell packages out of PVC [polyvinyl chloride], so, when we started forming in PET, we learned a lot of hard lessons,” Dan says. “It didn’t bend the same way, it didn’t form the same way, and we needed to adjust a lot of processing and tooling. With a lot of learning over a hard couple of years, we got to the point where it was second nature.”
Dan says Placon was able to supply its postconsumer PET for all of the fastener packages at Walmart through its customers Alco Fasteners and Anchor Fasteners.
Placon was riding the crest of the green wave. “Recognizing we had something unique, we decided that we might be able to market this to other customers,” he says. Customers soon had an option to have their clamshell packages made from PVC or postconsumer PET.
Many of those customers wanted the recycled content, and Placon improved its technology to make the cost of producing a clamshell package with recycled PET about the same as one made from virgin resin.
“The market was moving in a way that we thought that environmental concerns and sustainability was just beginning to take hold,” Dan says.
In 2001, Placon started buying recycled PET flake and extruding its own sheet on a new extrusion line.
It began selling food containers with 35 percent recycled content in 2008. The flake was not Food and Drug Administration approved, so Placon coextruded it with a virgin material layer in contact with the food. Now, EcoStar is approved for food contact, and Placon’s food containers are made with 75 percent or greater postconsumer content.
Closing the loop
Placon closed the loop when it built a processing plant in a former lumber company warehouse next to its headquarters in Madison, Wisconsin, and turned it into a recycling facility. Placon sorts, washes and processes bales of postconsumer bottles into PET flake that can be used in new EcoStar sheet.
“The recycling factory was an extension to vertically integrate and produce our own flake from postconsumer recycled bales,” Dan says. “We wanted to secure a better source, and the way to do that was through our own recycling factory. It was both cost and availability of the resources that we wanted.”
Placon invested $16 million to convert the building and to buy necessary recycling equipment.
“We were sourcing flake from all over the world, and it just really wasn’t meeting our quality requirements,” Dan says. “That caused us to look at technology to build the recycling facility.”
Dan says Placon executives spent two years talking to equipment suppliers and visiting recycling facilities in the U.S., Europe, Mexico and China to learn about recycling equipment. “We learned from equipment vendors as well as the recycling factories about how we wanted to engineer our EcoStar facility.”

Placon eventually settled on Italian machinery manufacturer Sorema Plastics Recycling Systems to manage the project and supply all the equipment.
Baled material enters the system on an in-feed conveyor that goes through a bale breaker. The next stop is a prewash station that tumbles the bottles and washes them with steam and a cleaning solution to remove labels, glue and dirt.
A SpydIR-ES optical sorter manufactured by National Recovery Technologies LLC, Nashville, Tennessee, uses laser sensors and cameras to remove non-PET and colored bottles from the incoming bottle stream. The bottles are then washed again with water and detergent.
A manual sorting station, typically manned by four people, catches anything that slips through the automated process.
Next, a wet grinding unit processes the bottles and thermoformed containers into flakes.
Some flakes at this stage go through a second hot wash to make them suitable for food-contact applications.
The next step uses tanks to separate cap and ring material from the PET flake. The flake sinks, while the cap and ring material is skimmed off the top.
The remaining flake is rinsed, dried and tested. Before being bagged, it goes through a Satake flake sorter, which removes any colored flakes that might have slipped through the process. The remaining flake is then extruded through one of three Davis-Standard extruders into clear, thin-roll stock for new packaging.
The company cleans and reuses process water. The recycling plant runs 24/7 and employs 50 people. It has a total capacity of 36 million pounds per year, which exceeds Placon’s current in-house demand.
Placon’s original business plan was to sell excess EcoStar material. “We had a major flaw in our original costing models having to do with the yield from the bales,” Dan says.
It turned out that the PET bales sometimes yielded as little as 45 percent of the bale’s weight in flake. “We underestimated the yields coming in, and we thought we would have a profoundly different cost structure, and that was one of the big mistakes we made,” he says.
“We weren’t able to get an acceptable price for the material, so we decided we did not want to compete in that space. We sold it on the outside initially just to build volume, but quickly decided that wasn’t a market for us.”
Dan says the company decided to produce only what it needed and to commercialize EcoStar through its thermoformed packaging. “That’s how we add value, and that’s how we differentiate in the thermoforming space.”
“A long-term play”
Has the investment in the recycling facility been worth it?
“Right now, I would say yes, but for years it was very much in question,” Dan says. “It wasn’t an instant moneymaker, and it is still a little bit questionable. I think strategically we always knew, and I am a really firm believer in what we are doing.
“We did it for a long-term play. We really believe that if our industry is going to exist in the future, there are a lot of challenges. One of them is the green aspect or sustainability. This is good for our industry. It’s good for us.”
Dan says Placon always wanted to be a leader in sustainability and has stuck with it even when in-house recycling did not add to the bottom line.
“In the last year, I felt like a switch was flipped and that all of a sudden the hard work that we have done for years is starting to be recognized and we can commercialize it,” he says.
“People are starting to come to us. When we first launched food-grade material, I thought customers would beat a path to our door. But it was more of a slow trickle. It’s been a long road.”
What is ahead for Placon? The company recently announced a circular economy partnership with SC Johnson. Placon will recycle plastic cups used at the Milwaukee Brewers’ Miller Park. The recycled flake Placon produces will be used to make bottles for SC Johnson’s Scrubbing Bubbles brand.
“We have other things in the works that we cannot announce right now, but we plan to be more active in taking back thermoforms and helping our customers meet their goals of reusing their own materials,” Dan says.
“Strategically, what we are doing is extending the circular economy to actually extract materials from the areas that we are selling into.”
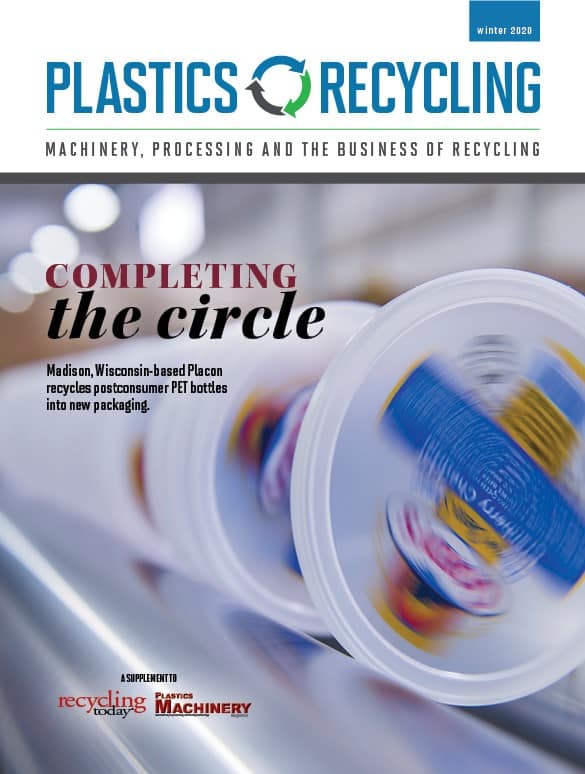
Explore the Winter 2020 Plastics Recycling Issue
Check out more from this issue and find you next story to read.
Latest from Recycling Today
- Meeting the decarbonization challenge
- Cyclic Materials expands leadership team
- Paper cup acceptance at US mills reaches new milestone
- EPA announces $3B to replace lead service lines
- AMCS showcasing Performance Sustainability Suite at WasteExpo
- New Way and Hyzon unveil first hydrogen fuel cell refuse truck
- Origin Materials introduces tethered PET beverage cap
- Rubicon selling fleet technology business, issuing preferred equity to Rodina Capital