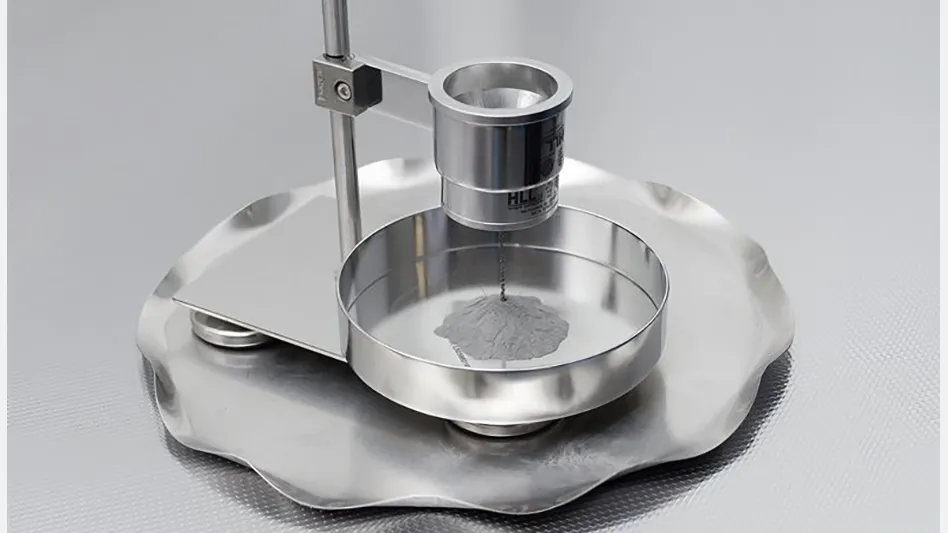
Photo courtesy of Outokumpu Oyj
Finland-based Outokumpu Oyj is entering the metal powder business for additive manufacturing and will include scrap materials in its production process, which will take place at a new atomization plant in Krefeld, Germany, that will start up this April.
The company says its metal powder production will further strengthen its sustainability strategy and circular economy efforts by using regional production scrap “to create new solutions to the market.”
Outokumpu says metal powders used for additive manufacturing (also known as 3D printing) are “revolutionizing the industry by boosting production capabilities through innovation and sustainability.”
“The global demand for metal powder is on the rise, and we see great potential for the business in the near future,” says Thomas Anstots, president of the advanced materials business line at Outokumpu. “We have seen the growth of additive manufacturing industries and the potential to strengthen the position and use of stainless steel for metal powder products and therefore decided to start the construction of a new designed atomization plant.
“Outokumpu has an extensive expertise on the materials and will partner with interested powder customers. We are happy to start with the internal production soon, followed by external run a bit later. There is already a great interest among customers and the first projects have started.”
Outokumpu says it will focus on producing metal powders that are not yet on the wider market and that are suited for companies that use technologies such as additive manufacturing (3D printing), metal injection molding, binder jetting and hot isostatic pressing to produce parts for demanding applications.
“In the near future, the estimated total production capacity [in those sectors] will be approximately 330 tons annually,” Anstots says. “Our longer-term target is to utilize the learnings and to build up our R&D know-how to support the customer journey with expertise, new material development, flexibility and customization for various powder metallurgy technologies. In our future vision, we could be able to serve our customers in such a way that they could come to us with a problem and leave with a solution.”
Outokumpu says the stainless steel it produces has the world’s highest recycled material content rate, reaching 94 percent last year. It refers to its mills in Europe and the United States as “among the largest material recycling facilities in the world" and says it will be aiming for maximum sustainability on the powders front.
“We want to help our customers to reduce climate burden by means of the right material choices,” Anstots says. “I’m proud of the fact that our new atomization plant in Krefeld will be a large recycling unit to support the circular economy further. The embodied carbon footprint of our whole production process is also reduced as the raw material is generated, and the product is produced and packaged, all in one place. This ensures to control the entire process and to significantly cut down the transportation emissions, too.”
Outokumpu's new portfolio of metal powders will include stainless steel and nickel alloys that have been “specially formulated to meet the demands of modern manufacturing in terms of quality, sustainability and flexibility.”
The metals producer says it is partnering with Germany-based SMS Group as its technology supplier in Krefeld. An equipment as a service (EaaS) contract “ensures a continuous line optimization and close collaboration in the powder business between the supplier and the producer over the next years,” Outokumpu says.
Latest from Recycling Today
- Connect Work Tools names new service manager
- Aaron Industries expands color capability
- Massachusetts voters support modernizing state Bottle Bill
- Oceana Canada poll shows support for single-use plastics ban
- Enviri releases annual ESG report
- Umicore sees lower revenues across all business groups for first half of year
- NEO Battery Materials, Lotus Energy Recycling to partner
- Partnership aims to convert industrial plastic scrap to synthetic graphene