
Photo courtesy of Cox Automotive
As electric vehicles (EVs) become increasingly prominent, the need for sustainable recycling processes for their batteries has never been greater. Cox Automotive is at the forefront of this movement, pioneering new and environmentally friendly ways to recycle batteries. One particularly exciting development is the dry battery recycling process.
The three-pronged approach to battery lifecycle management
Cox Automotive categorizes incoming batteries into three key areas:
- Remanufacturing – Batteries still capable of high performance are repurposed.
- Second life – Batteries useful for energy storage systems or other less-demanding applications.
- Recycling – No-longer-useful batteries are sent for recycling, particularly using our dry recycling process.
What is dry battery recycling?
Dry battery recycling is an approach that omits the use of water and chemicals commonly found in traditional battery recycling methods. This less energy-intensive method has a reduced carbon footprint and produces no liquid discharge, minimizing environmental hazards.
The development of environmentally friendly battery recycling methods is an ethical imperative—this is about being part of something special and leaving the next generation a better planet.
The process
The dry battery recycling process involves a number of steps:
- Sorting and inspection – Batteries are sorted based on type and condition.
- Disassembly – The battery packs are disassembled to separate valuable materials such as copper, aluminum and black mass (a mix of lithium, manganese and cobalt).
- Shredding – The disassembled components are shredded into smaller pieces for easier processing.
- Separation – Sorting of the metallic and nonmetallic materials.
- Purification – Any remaining impurities are eliminated using mechanical methods, avoiding chemical treatments.
- Preparation for reuse – The separated materials, especially black mass, are prepared for direct recycling.
- Quality control – All recycled materials undergo stringent quality checks before entering the manufacturing stream for new batteries.
A green & safe solution
Traditional battery recycling methods often employ chemical treatments and high-energy-consuming techniques. In contrast, dry recycling methods are less energy-intensive and do not use chemicals.
Here are some additional reasons why dry battery recycling is more environmentally friendly:
Reduced carbon footprint – The energy-efficient nature of dry recycling processes contributes to a reduced carbon footprint.
Zero liquid discharge – Dry battery recycling does not require water, eliminating the need for wastewater treatment.
Reduced hazardous waste production – The process is substantially cleaner, which makes disposal easier and safer for the environment.
Resource efficiency – Direct recycling of components such as black mass into cathode active material (CAM) for new batteries can be more efficiently accomplished through dry processes, saving valuable raw materials.

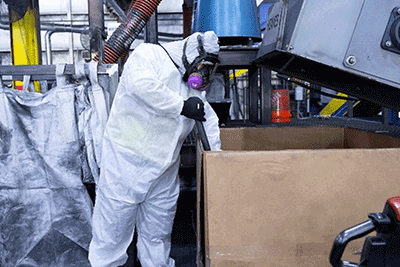
An additional benefit of the process is safety.
“Our proprietary process makes any risk of fire very unlikely,” says Juan Valencia, the director of Environmental Health and Safety with Cox Automotive EV Battery Solutions.
“One of the main reasons why lithium-ion batteries can catch fire or fail is thermal runaway,” he explains. “This process can occur within the battery if it becomes too hot, and it causes a chain reaction that can ultimately lead to a fire.
“During the thermal runaway of a battery, the chain reaction vaporizes the organic electrolyte and pressurizes the cell casing. If or when the case around the battery begins to fail, the flammable and toxic gases within the cell are released.
“Therefore, the fundamentals to reducing and/or eliminating fire risk for dry recycling processes are preparing the material before it is sent to the recycling process. Cox Automotive EVBS has developed those processes and proprietary technology to protect the safety of our employees, facilities and the communities that we serve,” Valencia says.
Meeting the emerging need
Electrification is going to drive recycling and vice versa. You can't have one significantly in front of the other.
Cox Automotive is setting the pace for an eco-friendly future in battery recycling. The dry battery recycling process stands out as a leading example of how we can balance technological progress with environmental sustainability. As the EV market grows, we are collectively responsible for supporting and investing in green recycling solutions.
Brian Skalovsky is director of battery recycling at Cox Automotive. Learn more here.
Latest from Recycling Today
- Researchers look into ironing out a secondary aluminum limitation
- Analysis: Chemical recycling’s ‘inflection point’ nearing
- Machinex system in Québec targets organics diversion
- Northern Shenandoah region awarded $3.9M for recycling infrastructure
- Eastman, Lubrizol improve adhesion strength of TPEs using sustainable materials
- Cyclyx receives ACC Sustainability Leadership Award
- WM updates Pittsburgh Recycling Facility
- LRS adds robot on its last-chance line to target UBCs