

Investment analysts and executives in the scrap-fed electric arc furnace (EAF) sector have made note of the profitable results and positive momentum that have characterized the industry the past several years.
EAF steel producers with cash on hand and positive investor sentiment behind them have taken advantage of the conditions to announce multiple new steel mill projects.
An accompanying question, which seems to be receiving some answers, focuses on how many mills, including which type and which sites, will be idled or shuttered as new EAF capacity is introduced this decade.
Something planned, something sudden
In terms of replacing EAF capacity, one of the more planned mill phaseouts was undertaken by Texas-based Commercial Metals Co. (CMC) late last decade.
Earlier this year, CMC had been hinting at operating costs and California-specific regulatory requirements surrounding the EAF mill in Rancho Cucamonga, California, it had acquired in 2018.
By the time CMC announced in 2020 its intention to double capacity in Mesa, Arizona, essentially placing two EAF micro mills adjacent to each other, it already had idled production at its Rancho Cucamonga site. Subsequently, it has resold the land beneath the former mill complex.
EAF steel producer Nucor Corp., Charlotte, North Carolina, likewise has proved it is willing to identify production sites for closure as it adds capacity. Most of the announcements made by Nucor in the past five years have focused on new mill locations or investments in upgrades and modernization at existing sites.
However, the company announced in May it would halt production at its Longview, Texas, EAF mill, which it purchased in 2016, in what it said was part of a reorganization of its steel plate group.
When making the announcement, Nucor said the 100,000 tons of annual capacity at Longview could be reassigned to its recently opened mill in Brandenburg, Kentucky, and to other Nucor plants.
While those two closures largely could have been anticipated, the demise of the former Republic Steel EAF mill in Canton, Ohio, this summer seemed to catch some observers by surprise.
When contacted by a Cleveland-area media outlet, two union workers at the mill said the facility’s Mexico-based owner, Grupo Simec, had issued sudden instructions to quickly ramp down its production equipment.
Like CMC and Nucor, however, Grupo Simec said the idling of the mill was undertaken because it expected to be able to serve its customers while consolidating production of the special bar quality (SBQ) steel produced at its mill in Tlaxcala, Mexico.
The three closures, two undertaken this year, have resulted in up to 1.8 million tons per year of retired EAF capacity, serving to demonstrate new EAF capacity is more likely to be a shift in overall production rather than a large-scale expansion.
Breathing the same oxygen
Throughout the past several decades, the booming EAF sector was gaining much of its market share at the expense of the capital-intensive blast furnace/basic oxygen furnace (BOF) steelmaking industry.
Having largely cornered the steel reinforcing bar (rebar) space, EAF producers have continued to invest in and pioneer technologies to give themselves a larger share of the flat-rolled steel sheet market.
Both Nucor and Steel Dynamics Inc. (SDI), Fort Wayne, Indiana, operate plate mills and downstream equipment to make growing varieties of flat-rolled steel.
One of SDI’s largest investments in recent years was its flat-rolled mill in Sinton, Texas. CEO Mark D. Millett last year said the mill “represents next-generation, lower-carbon-emitting steel production capabilities providing differentiated products and supply chain solutions.”
The ability of EAF mills to exceed their current 70 percent or so of overall steel market share in the United States is uncertain, but the future of the remaining blast furnace/BOF assets is nonetheless a subject of speculation.
Each time a blast furnace is idled to conduct a relining—a maintenance procedure that entails a potential four-month shutdown of a furnace designed to run nonstop—operators typically are asked by industry analysts whether the furnace will indeed be restarted.
The two remaining blast furnace operators in the U.S.—Cleveland-Cliffs and United States Steel Corp.—largely have been profitable the past three years, but each has been confronted with determining whether to perform a relining.
This summer, Cleveland-Cliffs, headquartered in Cleveland, announced it was delaying a blast furnace relining project at its Burns Harbor, Indiana, complex, initially predicting a 2025 time frame for the maintenance work but later identifying 2026 as the likelier year.
Pittsburgh-based U.S. Steel decided to divest itself of two blast furnaces at its Granite City, Illinois, complex last year, instead making an arrangement with Illinois-based SunCoke Energy Inc. for it to produce granulated pig iron at the site.
Complicating the operating future of America’s blast furnace/BOF mills is an offer made by Cleveland-Cliffs to acquire U.S. Steel. As of mid-September, U.S. Steel’s board says it is considering bids made by Cleveland-Cliffs and others that could see further consolidation in an already small field of players.

Narrower profits, static output
Positive investment sentiment toward the steel industry and the decarbonization momentum behind recycled-content steel has allowed North American producers to upgrade the EAF sector’s capacity the past several years.
The new and planned EAF capacity ranges from Arizona to Arkansas to West Virginia and up into Canada. Economic data and steel output figures from this year, however, seem to show the upgrades have been about retaining market share rather than creating an overall bigger pie.
The U.S has not fallen into recession this year, instead enjoying modest economic growth. Yet, steel production and import figures in the U.S. portray a domestic steel industry struggling to match the 2022 pace of output or consumption.
“The U.S. steel industry has undergone meaningful consolidation in recent years, which we believe has improved supply discipline,” London-based Fitch Ratings says in a late-June analysis. “This [has] led to generally higher and more stable margins through the cycle. We view the Infrastructure Investment and Jobs Act, Inflation Reduction Act, and the Creating Helpful Incentives to Produce Semiconductors (CHIPS) and Science Act as supportive for U.S. steel demand.”
But while steelmakers have reported profits this year, they are largely narrower than what in some cases were record profits in 2022.
Nucor, for example, earned $2.6 billion in the first half of this year. As impressive as that figure is, it represents a 44.2 percent decline from $4.66 billion of net income Nucor earned in the first six months of last year.
In terms of output, steelmakers in the U.S. shipped 7.55 million tons of product in July, a 1.6 percent decrease from the more than 7.67 million tons shipped in July 2022, according to the American Iron & Steel Institute (AISI), Washington.
Year to date, domestic steel shipments of more than 51.86 million tons represent a 3.3 percent decrease from the 53.65 million tons shipped in the first seven months of 2022.
Offering better news, AISI reported in the week ending Sept. 2 that mill production in the U.S. of nearly 1.73 million tons increased by 1.2 percent from the nearly 1.71 million tons made in the comparable week in 2022.
Year to date, however, mill output through Sept. 2 was about 59.84 million tons, which is down 1.8 percent from the more than 60.9 million tons made in the same time frame in 2022.
As well, the U.S. mill capability utilization (capacity) rate has averaged 76 percent so far this year. That is a 4.6 decrease from the 79.7 percent average capacity rate in the first eight months of last year.
Whether for market or government policy reasons, data compiled by the U.S. Commerce Department show domestic steelmakers have claimed a larger share of the overall market so far this year.
Commerce Department Steel Import Monitoring and Analysis (SIMA) figures indicate steel import permit applications in August for about 2.21 million tons of shipments equated to a 3.2 percent decrease from the more than 2.28 million tons brought in in August of last year.
After the first eight months of this year, total (finished and semifinished) steel imports of slightly more than 19.59 million tons are down 10.9 percent from the same period in 2022. AISI says the estimated finished steel import market share in August was 21 percent while year to date it is 22 percent. The leading exporters of steel to the U.S. this year are Canada (4.7 million tons), Mexico (more than 2.9 million tons) and Brazil (nearly 2.7 million tons), according to AISI.
This year’s relatively stable steel output level has created an equally stable ferrous scrap price. To what extent new EAF capacity will change the equation is unclear, though changes might pertain more to shipping patterns and destinations than to overall scrap demand.
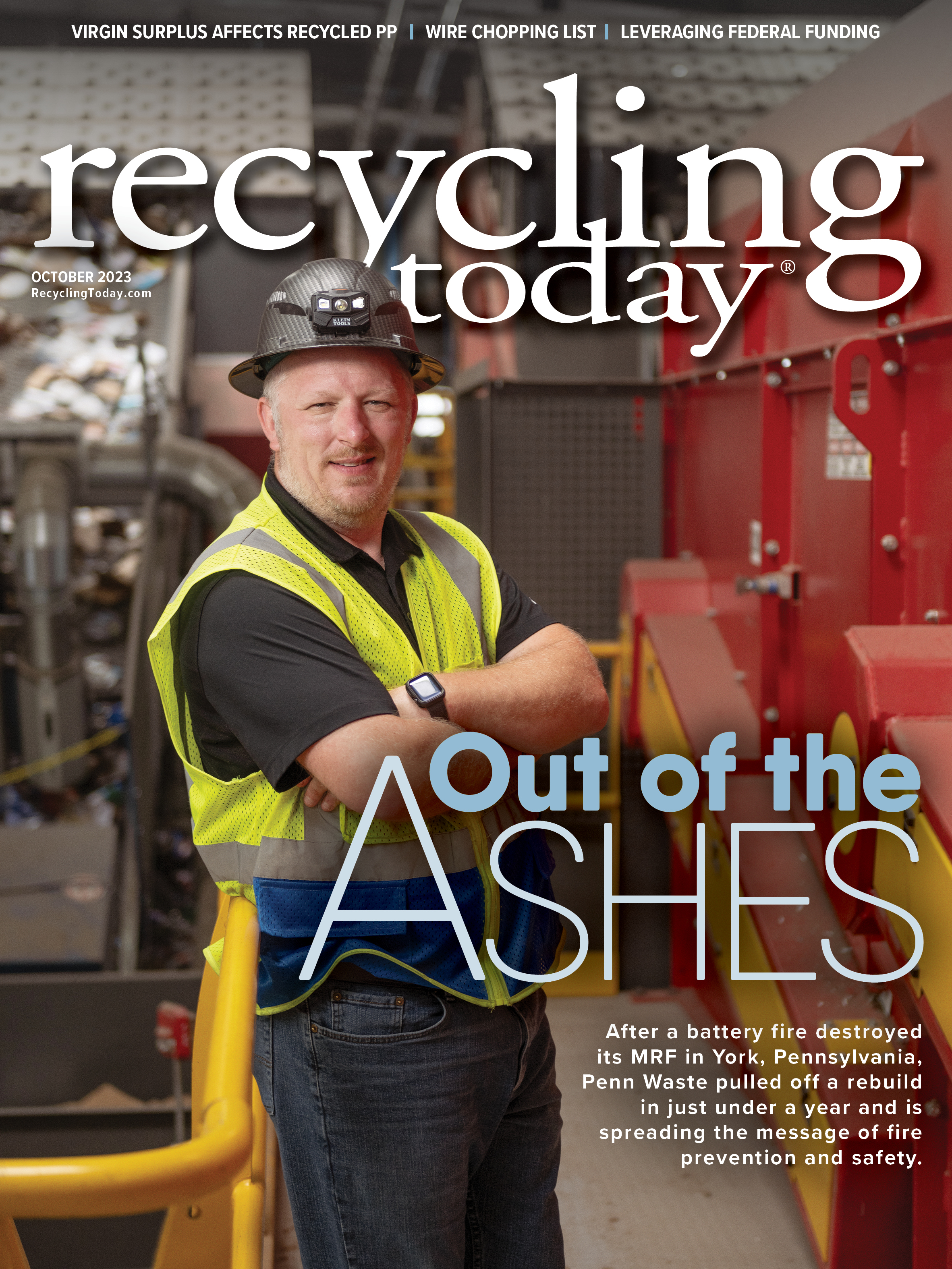
Explore the October 2023 Issue
Check out more from this issue and find you next story to read.
Latest from Recycling Today
- Bridgestone introduces retreating plant virtual tour
- USTMA announces Tire Recycling Foundation
- Dow announces agreement with Freepoint and MOU for Asia Pacific market with SCGC
- Mixed signals chracterize ferrous market
- Researchers look into ironing out a secondary aluminum limitation
- Analysis: Chemical recycling’s ‘inflection point’ nearing
- Machinex system in Québec targets organics diversion
- Northern Shenandoah region awarded $3.9M for recycling infrastructure