To say Bayshore Recycling Corp. is not your traditional recycling business would be an understatement. From being a woman-run business to having its roots in highway contracting, the Keasbey, N.J.-based company is breaking the mold when it comes to recycling operations in New Jersey.
Its owners are the husband-and-wife team of Frank and Valerie Montecalvo. When the two met in the early 1980s, Frank was running a heavy highway construction company doing paving, milling, utility installations and storm drainage.
As the two fell in love and got married, they also realized they enjoyed working in business together. While Frank liked being out in the field overseeing the work of laborers and equipment operators, Valerie preferred being in the office handling human resources, accounting, legal work and permitting.
Valerie is proud of the fact that, as owners, she and Frank are “very hands-on.” Occasionally in those early days of being in business together, Valerie, who now serves as president of Bayshore, would venture out into the field to see what Frank, now chief operating officer of Bayshore, and his crew were up to. “I was always very inquisitive and asked a lot of questions,” she says.
During these excursions to job sites, Valerie remembers thinking how much of the valuable material generated on the projects was hauled to landfills.
“I drove with Frank in one of our trucks to see what the landfills looked like, and I was very taken aback at the volume of waste generated in Central New Jersey alone,” Valerie remembers. Living and working in the hub of New Jersey’s urban area, only 30 miles from Manhattan, Valerie and Frank were seeing valuable commodities being discarded in dumps in staggering volumes.
“As manufacturing waned and environmental rules became stricter, there were many abandoned, contaminated industrial properties,” says Valerie. “I thought, perhaps we can purchase one of these large brownfield properties for future development and venture into the recycling business.”
Getting Started
Frank and Valerie weren’t sure how to get their recycling business off the ground, but the two always wanted to enhance their contracting company by being a material supplier. “One day we saw another contractor crushing concrete and asphalt and making stone,” recalls Valerie.
In the mid-1990s, the Montecalvos were working on a project that involved two large industrial roads. Valerie says they convinced the engineers they could do the job in half the time and at a much lower cost if the engineer would allow them to recycle the asphalt and concrete.
Bayshore Recycling Corp. Eco-Complex and Energy Park affiliated businesses
Bayshore Soil Management LLC (BSM): Accepts up to 3,500 TPD of nonhazardous petroleum-contaminated soils and operates a low-temperature thermal desorption unit Montecalvo Material Recovery Facility (MMRF): This 1,000 TPD facility opened in April of 2010 and accepts mixed construction & demolition debris, including paper, mixed plastic, corrugated cardboard, ferrous and nonferrous metals, aggregate materials and different grades of wood Coastal Metal Recycling Corp.: Accepts scrap metal, including, copper, brass, pipe, aluminum, stainless steel, wire and steel Dredge Material Processing: Permitted to store 143,000 cubic yards of material to a height of 40 feet Consumer Electronics: Accepts computers, monitors, scanners, modems, printers, cables, keyboards, televisions and telephones Class-A Recycling Facility: Currently accepts all materials placed curbside by homeowners, businesses and institutions, including aluminum cans; glass bottles and jars; steel and tin cans; plastic milk, water, soda and laundry bottles; newspaper; corrugated cardboard; textiles; and mixed paperl; has proposed accepting plastic materials coded 1 through 7 |
“The roads were concrete-based and covered over with asphalt,” says Valerie. “We convinced the engineer to let us pilot a program to recycle the material at an adjacent parking lot right next to the project and reuse it once it was processed to meet the appropriate engineering specification.”
She continues, “We made an aggregate road base material out of all the asphalt and concrete excavated out of the project.”
To this day, Valerie says, “Those roads have not been resurfaced or redone and have held up incredibly well despite the heavy industrial traffic of the area.”
While that first project proved successful, the Montecalvos still had tough times ahead before the use of recycled aggregate would be more widely adopted. While Valerie says the New Jersey Department of Environmental Protection (NJDEP) liked the project, the agency did not find it appropriate to crush material on site in every instance, mostly because of the dust and noise that could result.
“The folks at the NJDEP favored centralized recycling facilities as opposed to on-site processing,” Valerie explains. Many of the projects the Montecalvos wanted to pursue were in residential neighborhoods where on-site recycling was prohibited. So they began searching for property that would allow them to recycle aggregate on a large-scale basis.
The Early Days
Frank and Valerie initially began recycling operations on two small industrial properties where they would process material they generated from their own job sites. “When word got around that we were doing this successfully, many of our competitors in the road contracting business soon became our clients,” Valerie notes.
Still, it wasn’t all smooth sailing, as recycling wasn’t as widely accepted as it is today. The Montecalvos experienced obstacles from municipal engineers who were concerned with the routine use of recycled aggregate products.
“A lot of the engineers felt there wasn’t enough data to support the integrity of recycled aggregate products over time when compared to roads constructed with virgin products,” Valerie explains.
While it was difficult to convince the public sector that recycled materials were equivalent to virgin materials, private contractors saw the economic value.
“As long as the engineering specifications were met, builders and developers were comfortable utilizing this material,” says Valerie. In addition to the environmental benefits of using recycled aggregates, the private sector also saw a cost savings. Instead of transporting virgin material from a quarry located 40 to 50 miles away, contractors were able to cut their transportation costs in half, according to Valerie.
“The reduced project costs and environmental benefits of using recycled products were amazing and allowed us to eventually catapult into an exponential growth stage,” she says.
Building a Portfolio
In 2000, the Montecalvos purchased 26 acres of property on a former industrial site in Woodbridge Township, N.J.; about four years later, they purchased another 26 acres. They have leased an additional 10 acres and are hoping to add another 35 acres in the near future. Today, several businesses are located at the 55-acre Eco-Complex and Energy Park.
“Bayshore Recycling Corp. was the business that started it all,” Valerie says. The company is permitted to receive 2,500 tons per day (TPD) of concrete, asphalt, brick and block.
Soil remediation has been another successful venture for the team. Bayshore Soil Management can accept up to 3,500 TPD of nonhazardous petroleum-contaminated soils. A low-temperature thermal desorption unit is operating at the indoor facility.
A Woman’s Touch Valerie Montecalvo, president of Bayshore Recycling in the Keasbey section of Woodbridge Township, N.J., understands that her role in the recycling and highway construction industry is nontraditional for a woman, but that in no way intimidates her. “I mentor many young women both in and out of my industry. Basically, we are all about working hard while still embracing our femininity and intelligence,” she says. “Why can’t we enjoy dressing up and wearing makeup in this industry or any other?”
“I think if you love what you do and have a passion, you will earn others’ respect,” Valerie states. “I think being a woman has helped me break barriers, and stereotypes. ‘No’ was an answer I was just not willing to accept.” Montecalvo is currently president of the Construction & Demolition Recycling Association (CDRA), the national association representing C&D recycling, and is the first woman to hold the post. “Beyond the exciting path our board of directors and past presidents (of the CDRA) have set us on, being president of the CDRA has enormous meaning to me,” Montecalvo explains. “Public consciousness of waste and recycling is continuing to encourage ‘green business practices’ like materials recovery and recycling of C&D debris. I have been blessed with an extraordinary career in this industry, and it is my hope that I can continue promoting the growth, acceptance and hopefully required practice of C&D recycling.” |
When excavated material is brought to the plant for remediation, it is dumped inside a building specifically fabricated for such a purpose. Then it is loaded onto a conveyor for introduction into a rotary kiln, where it is processed at a temperature of about 970 degrees Fahrenheit. The kiln volatilizes the petroleum hydrocarbons and frees the soil of organic contaminants. The processed material exits the machine, is rehydrated at a pug mill and mixed into several materials: aggregate, landfill cover or road base.
Montecalvo Material Recovery Facility (MMRF) was created in 2010 and is permitted to take 1,000 TPD of mixed construction & demolition (C&D) debris and bulky waste. The facility uses a fully automated recycling system manufactured by Premier Tech, Rivière-du-Loup, Québec, and a Continental Biomass Industries (CBI), Newton, N.H., 5400 horizontal wood grinder to grind certain wood for landscaping mulch. Approximately 20 to 30 people hand sort material on a picking line at the facility, which recovers about 75 percent of the incoming materials for recycling, including wood, paper, corrugated cardboard, metals, plastics and aggregate debris.
Because of stormwater requirements in New Jersey, C&D debris cannot be kept outside, so the Montecalvos salvaged part of the property’s original industrial superstructure to build MMRF. Two or three floors were removed in some parts of the building to allow for storing and loading of material inside.
Adulterated wood, paper, corrugated cardboard and plastics are turned into an engineered biofuel. “It is such an important end use for our material, because otherwise this material would probably be landfilled,” says Valerie.
Coastal Metal Recycling is the Montecalvos’ scrap metal operation. Permitted to accept copper, brass, pipe, aluminum, stainless steel, wire and steel, this material is currently allowed to be kept outside, but Valerie says one day it may be required to be moved indoors because of possible impacts to stormwater.
The Montecalvos also are permitted to remediate and stabilize dredge material. “Due to the historical industrial activity in our area, most of the sediment in our waterways is also contaminated, so there is a huge call for waterfront facilities that can remediate or stabilize dredge material for beneficial reuse,” says Valerie.
Bayshore hosted pilot programs in 2005 and 2006 aimed at remediating contaminated dredge material. The company even bought a 720-foot bulk carrier ship to serve as a staging platform for dewatering the contaminated material. “We demonstrated to the ports and the governmental agencies that the material could be safely handled and stored,” says Valerie, adding, “What the technology could not demonstrate at that time was that it was the most cost-effective way to remediate some of the more heavily contaminated materials.”
However, Valerie says there is some renewed interest and new funding available to look at severely contaminated sediments again, particularly in the Passaic River, where there is an interest in dredging the river to a navigable depth.
Valerie adds, “Bayshore’s location on the Raritan River, in proximity to the Port of New York and New Jersey as well as its direct rail access and close-by highways, position it well to take in dredge material by barge, stabilize it and send it back out by rail for use on highway projects, brownfield sites or landfills.”
When New Jersey’s electronics disposal ban went into effect in January 2011, Bayshore was strategically permitted to collect consumer electronics. The company applied to be a large-quantity handler. “Right now we just aggregate them and send them off to recyclers that demanufacture them,” Valerie says. “In the future, if we have any energy left, we might open up our own demanufacturing operation.” In the meantime, Bayshore is interested in attracting a tenant to handle the demanufacturing on site.
Snag in the Plans
Valerie characterizes the development of Bayshore’s recycling operation as a little bit backward. “We went into recycling the opposite way most people do. We started out with nontraditional materials: concrete, asphalt, contaminated soil.”
It wasn’t until last year that Bayshore received a permit for a Class A recycling facility, which is for the recycling of traditional curbside items, such as newspaper, cardboard and metal cans, generated by homeowners and businesses. The Montecalvos were preparing to launch the Class A operation when Mother Nature had other plans.
“We bought a single-stream system right before Hurricane Sandy hit,” Valerie explains. “It has been sitting in the crate since then.”
Bayshore is located about 6 miles from areas like Union Beach, N.J., and Staten Island, N.Y., which sustained major damage from the storm. “We were hit pretty badly by the hurricane,” Valerie says. “Our area of the Raritan River has not flooded in 150 years, but during Sandy, a 6- to 10-foot tidal surge came into our site.”
The superstorm filled Bayshore’s offices with nearly 6 feet of water and flooded the mechanic shop containing equipment. A spark was set off in the maintenance building and caused the shop to burn down.
“The building earmarked for organic recycling became a makeshift garage for equipment for our mechanics,” she says. Bayshore may construct a new building and has been accepting recyclables on a small scale from big-box stores in the area. Valerie says she expects the single-stream system to be installed and operating in early 2014. Despite the damage and delays, she doesn’t view Sandy as a total set-back.
Valerie says, “On one hand, it put a damper on our plans. But on the other hand, it generated an incredible amount of volume, which we were easily able to handle. While much of that material was not able to be recycled, we helped a lot of municipalities quickly and efficiently get material out of the way to start the rebuilding process.”
Fueling the Future
Energy conservation and renewable energy also are at the center of Bayshore’s business plan. The company installed 9,365 solar panels that produce 679 kilowatt-hours of electricity in 2008. Bayshore plans to add wind and biomass energy technology to its operations and to use the energy produced to complete its corporate vision to operate 100 percent green businesses powered by 100-percent-renewable energy.
Beyond these existing and planned operations, Valerie says Bayshore’s ultimate vision is to develop additional green industries that will advance sustainability and the aforementioned corporate vision.
Bayshore is reviewing several waste conversion technologies to help achieve this goal, including plastics-to-energy pyrolysis, food waste fermentation, anaerobic digestion, tires-to-fuel technology and various forms of gasification.
The Montecalvos’ daughter, Nicole, and son, Frankie, have grown up in the recycling business, and both currently work at Bayshore to continue their parents legacy to bring recycling into the next generation.
“It’s amazing how one small idea of recycling the concrete, asphalt, brick and block generated at a job site can blossom into what we like to call our Eco-Complex and Energy Campus,” Valerie proudly says. “Now we have seven different entities that are all fully permitted to recycle recoverable commodities, each operating synergistically with the others.”
This feature originally ran in the November/December 2013 issue of Construction & Demolition Recycling, a sister publication of Recycling Today. The author is managing editor of Construction & Demolition Recycling and can be reached at ksmith@gie.net.
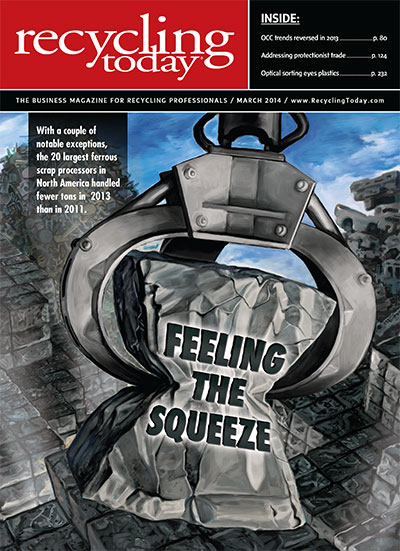
Explore the March 2014 Issue
Check out more from this issue and find you next story to read.
Latest from Recycling Today
- Plastic packaging report finds gaps in companies’ commitments, actions
- Trumpf develops laser processes to recycle EV batteries
- Clarios highlights recycling efforts in 2023 sustainability report
- Call2Recycle appoints new board chair
- A bright future on the demand side
- Voith increases operating results in 2023-24 fiscal year
- Local organizations partner for composting pilot program
- Tenaris commemorates 20 years of steel recycling in Romania