When scrap recyclers reach a point where they can install a large, stationary ferrous baler, they are making a considerable investment in processing machinery.
Machines designed to compress and shear thick, tough grades of ferrous scrap carry a hefty price tag that reflects not just the size of such machines, but also the level of sophistication.
The large processing machines consist of several mechanical systems and a number of components with narrow operating specifications that make these multi-ton machines more vulnerable than they appear at first glance.
Terry Clark is a field service manager with FEMCO Machine, Punxsutawney, Pa., a company that specializes in the installation, maintenance and repair of heavy industrial equipment.
In his three decades of experience, Clark has seen “the good, the bad and the ugly” of how these stationary ferrous balers can be maintained and operated by their owners.
In an interview with Recycling Today’s Editor-in-Chief Brian Taylor, he provides some tips that could help ferrous baler owners extend the lives of their machines as well as some cautionary advice on behaviors to steer clear of to avoid sudden equipment failure.
Recycling Today (RT): What are some common problems that can make a baler less productive?
Terry Clark (TC): A common problem we see is that many companies run their machines beyond the standard recommended time for liner changes, and the liners will then wear out beyond their standard thickness. Normally, liners should be changed every two to five years, depending on the tonnage and the material being baled.
For many of our accounts, we perform a scheduled baler preventive maintenance program. This is a full-day inspection, most commonly done every six months.
Regular maintenance inspections are a great preventive maintenance rule of thumb. In the downturn, many people and companies are going to do what they can with what they have; they spend less money. But normally, when times are good, they will do what it takes to maintain and even rebuild their balers and shears.
What happens is that the thinner the liner gets, the more prone the rams become to jamming. Material gets stuck under the header of the gather ram. Loose material there or at the bottom of the ram will jam at the header.
Any one of those compression rams can actually pick up a piece of loose material—we call it a sticker. That sticker will wedge itself underneath the side, top or bottom of the ram. Stickers then get pushed and jammed into a position where they can go no further. Then, normally, rams go in reverse but you can break off the button of the cylinder rod. The bigger the machine, the more costly the repair then becomes.
For, say, a second compression cylinder in a large baler, you need a big crane to do the repair. The repair process is difficult because you can’t even fix it in the field. You have to disassemble the whole cylinder and take it to a machine shop.
Since FEMCO has a machine shop, sometimes we will bring in the whole machine, in disassembled components, and then inspect and evaluate every component. This helps us determine the problems and then notify the customer, who will come in and determine what’s critical to be fixed and what is not.
RT: What are the harmful outcomes of using a baler that is too small or light-duty for the volume of work a recycler is doing?
TC: Normally what happens there, and it happens all the time, is that a lot of smaller balers meant for nonferrous metals are used by companies to bale ferrous material. Normally, if the machine is not the right kind for that type of material or tonnage, it may over time develop major structural cracks to the main frame itself or in the charging box or the press box area. Also, what can occur is overheating of pumps and hydraulic components.
RT: When the operator is inattentive to what is being fed into the baler, what are some of the worst-case results?
TC: It varies. Companies are not baling cars nearly as much as they used to. But they still get compressed this way, and when they do, operators should look in the car and trunks first. Propane tanks that are compressed will explode.
Another common problem is, when an operator is not paying attention, you’ll get a large piece of heavy plate that will be dumped in there. From that point, there is not enough compression force, and you’ll have the same problem as if too much material has been introduced, but in this case it’s too dense.
In this situation, often they’ll call us and our field service people will come out with hydraulic equipment—250-ton hydraulic rams to try to break this loose—and then try to disassemble the machine at the point where it’s jammed, usually the third compression ram.
When you’re baling heavier material, like a 4-foot-by-8-foot piece of plate, something has to give. If you don’t have enough force to make the bale, something will break—either hydraulically, like a cylinder rod, or it could push a liner off the floor or pull liners from the rams or off the press box or charging box. This can destroy the liners.
RT: What are some behaviors that can result in a fatal or serious worker accident involving a baler?
TC: The most important safety factor on any machine, including balers, is that many people do not enact a lockout/tagout procedure on the electrical boxes and they don’t shut the machine down for a quick task. Their thinking is, “I’m only going to be doing this for a couple of minutes.” But the most important thing is making sure the machine is completely shut down and all electrical boxes have a lockout/tagout on them.
As a field service person for 30 years and now with a crew of from 12 to 20, I tell them each time they head out to be safe, watch out for themselves and watch out for other people.
FEMCO has a good safety program we offer to customers—in my eyes it’s as good as anybody’s in the country.
RT: Can inattention to cleanliness result in bad outcomes, and if so what are some of those?
TC: One of the things I’ve noticed over the years is cleanliness is definitely an important factor in safety. Large ferrous balers have pump rooms because they have considerable hydraulic fluid needs and they store hydraulic oil in a large tank. In some customer facilities, you can literally go into their pump room and drop something on the floor and there is not a speck of dirt or oil on it. Unfortunately, I’ve also gone into pump rooms with three pallets stacked on top of each other so you can make your way across the room.
Cleanliness in a pump room is critical. Those rooms get a lot of heat in there. What could occur with both electrical wiring and a lot of oil in there is you could have a fire. And safety regarding slipping is clearly another factor.
Also, the cleaner the machine is, the easier it is to spot a hydraulic leak or any other repair that needs to be made.
RT: What are the most common causes of hydraulic cylinder failure?
TC: This certainly relates to maintenance and cleanliness, because most of the time it’s fluid contamination—the hydraulic oil gets contaminated. I have a situation like that happening right now. It’s a serious situation happening to a machine that is not very old. It’s a very costly problem.
Normally, the best way to prevent this is to have a good preventive maintenance program. Someone becomes responsible for the periodic testing of oils. If they have a setup on a computer to record this data, they can keep a running track record on what is happening with the machine. It is a good way of preventing the type of fluid contamination that can scratch a cylinder from happening.
Our preferred way to work at FEMCO is to instruct people not only how to run a machine but also how to maintain it. The longevity of the equipment really depends on doing that. When you have a contamination problem, it affects the whole machine. Every cylinder then has to be torn down and cleaned and all the pipes have to be washed.
In a bullish market or a slow one like today, I believe inspections are critical so company owners know what could be coming up in terms of needed repairs. When these aren’t performed, they run the risk of running the baler and not knowing there are cracks or other problems that could really lead to high costs a few weeks or months down the road.
FEMCO field service manager Terry Clark can be reached at tclark@femcomach.com.
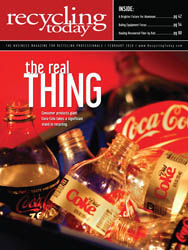
Explore the February 2010 Issue
Check out more from this issue and find you next story to read.
Latest from Recycling Today
- BGL report finds solid foundations for sustainability investments
- Bridgestone introduces retreating plant virtual tour
- USTMA announces Tire Recycling Foundation
- Dow announces agreement with Freepoint and MOU for Asia Pacific market with SCGC
- Mixed signals chracterize ferrous market
- Researchers look into ironing out a secondary aluminum limitation
- Analysis: Chemical recycling’s ‘inflection point’ nearing
- Machinex system in Québec targets organics diversion