
It is still early in the process, but First Star Recycling could be onto something.
Can a material recovery facility (MRF) capture items considered hard to recycle and convert them into salable end products under one roof? It is precisely the question First Star, based in Omaha, Nebraska, is attempting to answer.
Since opening its plastics recovery facility (PRF) March 1, the company has found success taking plastics that typically are landfilled or incinerated, ranging from food bags to foam cups and toothpaste tubes, processing them into pellets and flake then recycling them into lumber for decking, patio furniture and more.
As it continues to ramp up its project with the help of a $1.35 million loan and guidance from the Singapore-based Alliance to End Plastic Waste and the Hefty ReNew bag program sponsored by Dow Chemical Co., First Star is on its way to creating a truly circular economy for plastics that traditionally have not had strong markets.
“It’s probably something that’s always been in First Star’s psyche, so to speak,” says Danielle Easdale, director of sales and marketing at First Star. “I think becoming an end market as well as a recycler is something that has always been what First Star has looked to do.”
Origins and orange bags
First Star got its start in 1998 in Fremont, Nebraska, and has since expanded to become the city of Omaha’s contracted recycling hauler. Additionally, the company offers education and outreach to help businesses, organizations and communities understand the importance of recycling, as well as providing recyclables marketing and brokerage, on-site recycling training for commercial customers, a zero-waste program for businesses and recycling and waste management grant-writing assistance.
The company’s Omaha site spans 360,000 square feet, employs more than 100 people and processes about 100,000 tons of material per year. It also operates a baling and transfer station in Lincoln, Nebraska, and provides its services throughout Nebraska, Iowa and Colorado.
In the Omaha facility, separated by several walls and a storage area, sits a 7,500-square-foot PRF and plastic lumber manufacturing equipment, parts of a plan put in motion in July 2021 when First Star announced a three-year collaboration with the Alliance to End Plastic Waste to develop the integrated recycling complex alongside its MRF.
Since the announcement, First Star has sourced plastics preprocessing equipment from multiple vendors and used lumber manufacturing equipment from Rivalries Corp. of Barrie, Ontario. But before much of the hard-to-recycle material reaches those machines, it arrives at the MRF in bright orange Hefty bags customers can purchase at local grocery stores.
In 2016, Easdale says First Star became the first MRF in Nebraska to offer the Hefty Energy Bag program on a permanent basis. Initially, 6,000 households took part before it expanded citywide in Omaha, and Hefty—under the umbrella of Midland, Michigan-based Dow—gave the program its name because the bags, which were filled with hard-to-recycle items, would be sent to various sites to be converted into energy.“That program [in Omaha] was initially designed for the bags to be sent for energy recovery in the cement-making process as a coal alternative,” Easdale says. “Being recyclers, we like turning things back into new things. Once [bag contents] go through the cement-making process, that’s it.”
First Star wanted to find a way to keep those materials in the economic cycle, so it partnered with Hefty and Dow to find various end markets and technologies for the bags. “In that process, we started coming up with the concept of building the PRF and subsequent bolt-on manufacturing operations here at the facility,” Easdale says. “That was how the concept initially came about, and it’s been in the works for some time.
“We are going after plastics that didn’t have a market with traditional recycling before,” she adds. “So, things like the Hefty Energy Bag, agricultural film, other films or rigids that don’t have existing markets [are targets]. It’s a little different to what other PRFs are doing that are processing materials that have markets. This is going out to those harder-to-recycle materials. They are coming out daily through either the Energy Bag or other external sources.”
As new end markets have emerged for the contents inside the bags, Hefty has since changed the name of the program to Hefty ReNew.
Creating an end product
When loads of recyclables are dropped off at the MRF, the orange bags are removed from the stream by employees on the presort line and sent to the PRF. From there, material goes through a bag breaker and onto a sort line where contaminants such as metals are pulled out via a series of magnets and eddy currents.
After sorting, the materials are shredded, cleaned using a dry friction cleaning process, then pelletized or turned into what Easdale calls a “California cube,” a larger, denser, cube-shaped piece made from the recycled film. “It’s more of a larger cube, where the film’s densified but it’s designed to still be able to break up when they go into a remanufacturing process,” Easdale says. Of all the plastic the PRF processes, about 10 percent goes into lumber First Star manufactures. To turn the recycled material into the end product, it first is fed into a blender system, then extruded to a carousel that contains various die molds and creates different lumber profiles.
First Star CEO Patrick Leahy says the company is producing about 100 boards per day in four different sizes— 1-foot-by-6-foot, 2-by-6, 1-by-4 and 2-by-4—with the smaller sizes accounting for the majority of boards created each day.

The PRF is staffed with five employees working one shift per day, with three working on the PRF side aiding in sorting and two on the lumber side. First Star’s goal is to ramp up production so it can run three shifts per day and process 10,000 tons of plastic per year in the project’s first phase.
As part of that eventual ramp-up, First Star aims to process about 1.5 million pounds of material to create the lumber and make about 85,000 boards in the four sizes.
“We will scale up as [project] phases go on,” Leahy says. “It will depend on what we’re doing. The lumber operation is taking about 10 percent [of the material] from the PRF. So, there’s about 90 percent that is going into pellets and other options.”
Easdale adds that continuing to establish end markets is the key to the program’s success. Once enough lumber inventory is built up, First Star intends to sell it factory-direct or to smaller lumber yards, do-it-yourself deck builders and other small operations.
Future focus
As First Star continues to prove its business concept, the goal is to move into Phase 2, where the company will consider adding equipment to increase production to 20,000 tons of plastic lumber per year and attempt to find additional end markets for its pellets.
“Ultimately, what we’re trying to do is prove out the bolt-on manufacturing operations model,” Easdale says. “So, as we prove that out with Phase 1 and Phase 2, then we’ll be looking at varying options, varying technologies around the country of MRFs that may be interested in partnering with us to replicate this model in other places. There’s been a lot of interest, and people [are] watching to see how it shakes out.”
Leahy says the bulk of industry interest in First Star’s PRF and manufacturing venture comes from the pellet side of the operation. The lumber production side is the company’s current end market, but as the project progresses, others already are in mind.
Plastic pallets, railroad ties and roofing boards all have been discussed as future products that could be manufactured with First Star’s pellets. Regarding the pallets, Leahy says, “We have a vendor where we’re looking at their equipment right now and they’re doing some testing to see if it would be able to take hard-to-recycle plastics.”
He adds that even though plastic lumber and pallets are not new inventions, First Star’s use of hard-to-recycle material in their construction is more cutting-edge.
“When I heard plastic lumber, I kind of just shrugged and said, ‘OK, plastic lumber. That’s been done before,’” he says. “But this plastic lumber is very unique in that it’s not a composite and it’s not made of easily recycled plastics. It’s made of hard-to-recycle plastics and, in tests, it performs just the same in terms of strength. It’s something truly unique. … These will be very different because they’re made of the hard-to-recycle plastics, which is the true game-changer for a lot of companies in the industry.”
A go-to plastics recycler
Though the PRF and lumber manufacturing operations are still in an early phase, First Star is researching new feedstock and ways to help others in the industry find ways to convert hard-to-recycle plastics.
According to Leahy, First Star has begun testing agricultural films, or “ag bags,” to see if they can be used in the PRF/manufacturing process.
“Ag bags are an industry problem,” Leahy says. “Every state definitely has an agricultural base here in America, and these ag bags are getting used more and more by farmers, and they’re becoming more of a problem. So, we’re looking at that in Phase 1. We have some in supply right now that we’re going to test. If we can prove out these tests, then we hope that will also garner some attention as a possible solution for another problem.”
Leahy adds the company has been contacted by others in the industry about other types of hard-to-recycle plastics and has been sent samples for First Star to test in the PRF to see if it can make pellets or flakes to be used in the lumber operation.
“We’re happy to do that,” Leahy says. “We’re not just out there having conversations with end markets who will take the pellets and use a chemical or mechanical recycling process, but we’re also talking with folks who have issues with their offtake that we’re trying to help solve on a case-by-case basis. If we solve it, then perhaps it becomes a true circular thing, where we’re selling back to then remake a product.”
Easdale says she believes the project is beneficial from a consumer perspective as First Star has opened up the collection of a wider variety of plastics with the inclusion of the Hefty ReNew program.
“This is a great project, because now we’re not just taking No. 1 and No. 2 plastics,” she says. “Now, we’re developing something where you’re looking at almost all plastics. From a consumer point of view, and certainly for rural America as well, a lot of these programs haven’t been collecting plastics at all. So, this makes it a lot easier.
“The rural programs are able to collect their rigid containers. They can collect all the films and packaging, and that comes to our MRF,” she adds. “If it goes in the [ReNew] bag, it also comes to our MRF. And it makes it very easy for [municipalities] to establish recycling programs across the state and utilize hub-and-spoke systems where they can actually start to capture plastics in areas where it was either going to landfill or being burned.”
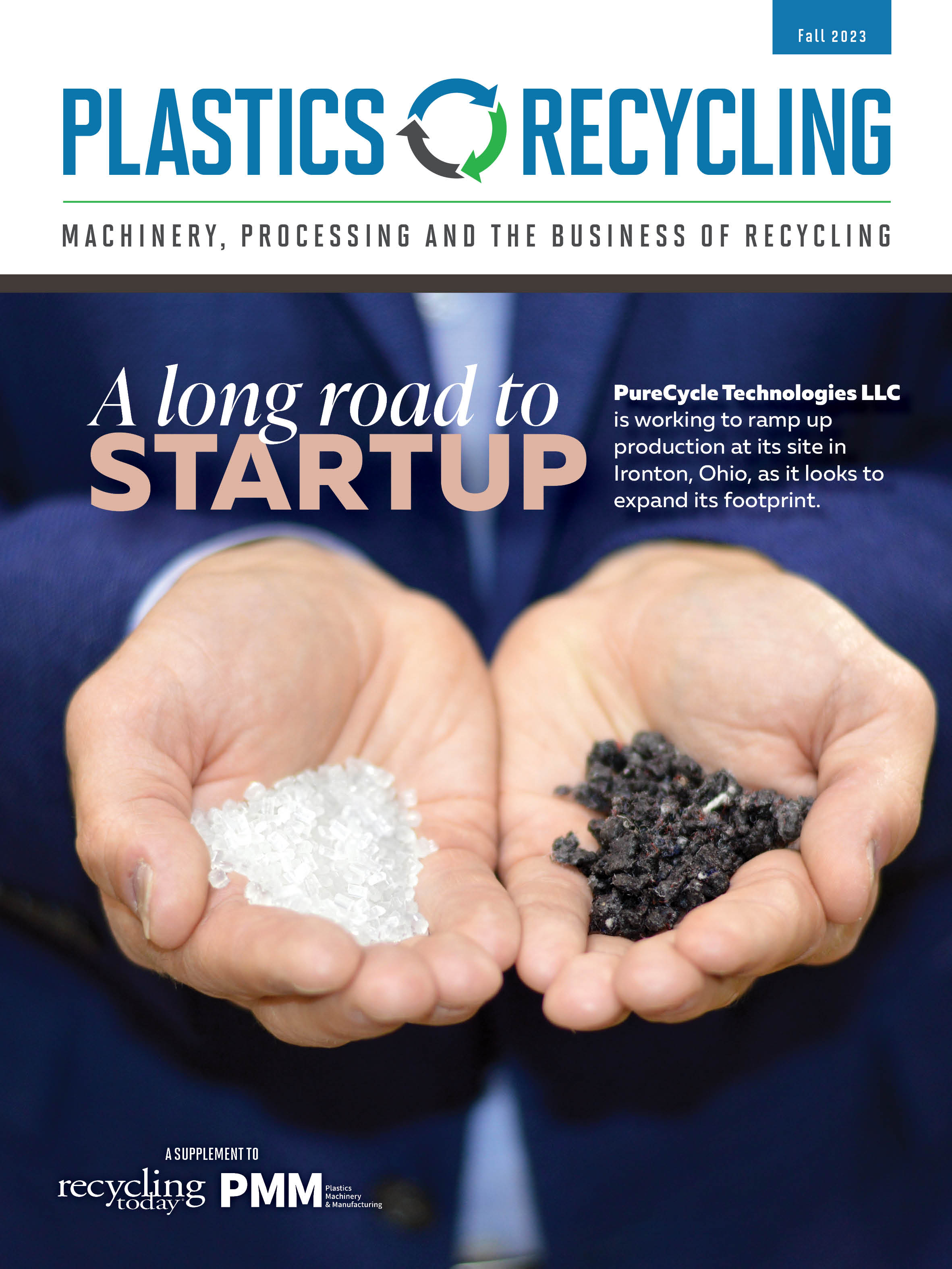
Explore the Fall 2023 Plastics Recycling Issue
Check out more from this issue and find you next story to read.
Latest from Recycling Today
- Domestic ferrous scrap market remains on ‘sideways’ trajectory
- GFL reports revenue increase in first quarter
- Guardian Data Destruction names new CEO
- Bulking up
- Greenmantra says polymer additives optimize customer’s HPDE pipe
- Pure Loop celebrates ISEC shredder-extruder at NPE
- New Alpla PET wine bottle cuts carbon emissions
- Ascend Elements, Call2Recycle to offer customized EV battery services