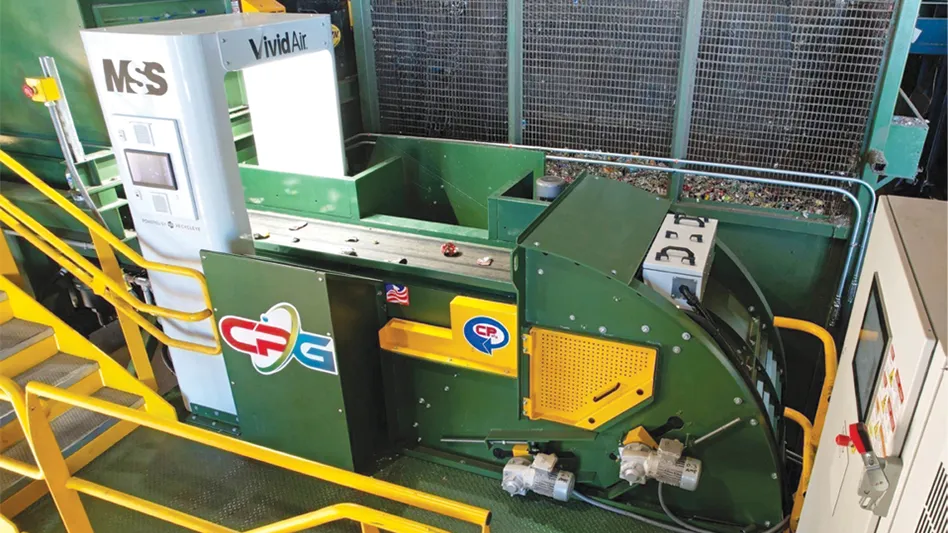

Recently, artificial intelligence (AI) and robotics have been getting a lot of attention. AI sensors combined with robotic arms were introduced to material recovery facilities (MRFs) around 2016-2017. Ever since then, a few hundred of these units have been installed in North American MRFs, many with mixed success on the extraction front. For some people, robotics and AI are synonymous. However, robotics is not AI, and AI is not robotics.
AI: Success!
The AI sensor aspect of these machines certainly has lived up to and even exceeded expectations. AI’s deep-learning capabilities and unmatched levels of available granularity provide finer classifications of individual product and material categories. AI sensors have identification capabilities beyond those of conventional optical sorters. They can be used to sort cat food cans and cooking foil from used beverage cans (UBCs) and polyethylene terephthalate (PET) thermoforms from PET bottles, for example. AI units that are used in similar applications also can learn from one another, creating even more robust AI models. This unique capability has further increased the accuracy and range of available material categories that AI technology can identify.
Robots: Fail!

The robotic arm aspect of these units, however, has been a much bigger disappointment, mostly given its limited speed, low picking efficiency depending on the commodity and high cost per pick.
The cost of replacing expensive suction cups every shift and the high use of expensive compressed air make the per-pick cost for a robotic arm 10 to 12 times more expensive than conventional high-pressure air ejectors used in conventional optical sorters.
Would you accept personnel whose sorting effectiveness was less than 50 percent for certain items? Probably not, but that’s what MRF operators often see when the suction system of a robotic arm encounters crumpled or 3-D items. Add that to the robotic arm’s inability to keep up with the required picks per minute, and sorting effectiveness for certain targeted materials can be less than 50 percent. That is not an acceptable level of performance in our view as we are held to much higher standards on conventional optical sorters.
Decoupling sensor technology from the extraction method
At MSS, we firmly believe that sensing needs to be completely decoupled from extraction because one has nothing to do with the other. The right detection technology, which can be a single sensor or a combination of them, must be paired with the most appropriate extraction method for the application.
We also know that AI is here to stay and will grow in prominence in recycling applications in the next decade, which is why MSS introduced Vivid Air™, our AI sensor platform, earlier this year in partnership with Recycleye, a U.K.-based AI technology company.
MSS Vivid Air™: A perfect pairing

While robotic arms will continue to be employed in tight retrofits and low-volume facilities where air jet units simply won’t fit, we don’t expect notable further progress in vacuum-based robotic extraction. This technology has changed little since its introduction to our industry about seven years ago.
Instead, MSS pairs established AI technology with our proven air ejection system that enables the sorting of material at higher throughput and without the limitations of robotic arms. Using established positive pressure air valves allows us to use wider belts where necessary and without the need for multiple parallel robotic arms. Belt speeds can be increased and pick rates boosted 10-fold over the same conveyor width to maximize throughput and sorting efficiency. And, as mentioned previously, compressed air valves require much less maintenance than mechanical arms.
Success story: Aluminum QC
One of the most prominent applications is sorting cat food cans and cooking foil from UBCs. At a recent installation on the West Coast, the MSS Vivid Air™ identifies the categories “UBC,” “Non-UBC Aluminum” and “Non-Aluminum,” ejecting “Non-Aluminum” separately from “Non-UBC Aluminum” and “UBC” in a dual-eject configuration. Should a particular market allow for “Non-UBC Aluminum” to stay with the “UBCs” then only a single-eject configuration would be required.
The Vivid Air™ ejector configuration is purposely designed to be very compact so it can be retrofitted on existing manual QC stations with minimal modifications.
Success story: PET QC
Another MRF application with great potential for Vivid Air™ is the quality control of near-infrared-sorted, or NIR-sorted, PET. In many cases, this application calls for the identification of the categories “PET Bottle,” “PET Thermoform” and “Non-PET.” Similar to the aluminum QC, the PET QC unit can be installed in a single-eject or dual-eject configuration, depending on available market outlets.
Other promising Vivid Air™ applications

Several other MRF and PRF, or plastic recovery facility, applications come to mind for the compact and versatile configuration of Vivid Air™:
- PE QC – Similar to the PET and aluminum QC, the QC of NIR-sorted PE calls for the identification and separation of the categories “PE Natural,” “PE Color” and “Non-PE.” These materials can be sorted separately from each other using a dual-eject configuration. Using a robotic arm for this application is not recommended as the required number of picks per minute by far exceeds the robot’s capability and the 3D-nature of PE bottles makes vacuum-based pickup very ineffective. Air jet arrays will ensure a high and accurate pick rate to prevent valuable PE Natural from ending up in PE Color, which would reduce the overall blended-ton value.
- Food grade (FG) PP from non-FG PP – AI really is the only sensor solution available for this application. While still challenging, AI’s ability to learn and become better over time means that sorting FG from Non-FG PP shows a lot of promise.
Perfected pairing
When automating manual QC lines, MRF operators should consider a technology platform that pairs the right type of sensor with the appropriate extraction method for the task at hand. Coupling AI with air jets, as is the case with the MSS Vivid Air™, provides the best of both worlds: identification capabilities that complement those of conventional NIR and color sorters, plus the proven compressed air jet extraction that provides higher belt speeds, pick rates, throughput and efficiency without the limitation and maintenance cost of a robotic arm.
Talk to a vendor that understands these nuances. We at MSS are ready to have that conversation with you.


Felix Hottenstein
Sales Director
MSS, Inc.

MSS, Inc.
300 Oceanside Drive, Nashville, TN 37204
615-781-2669 ext 215 | www.mssoptical.com
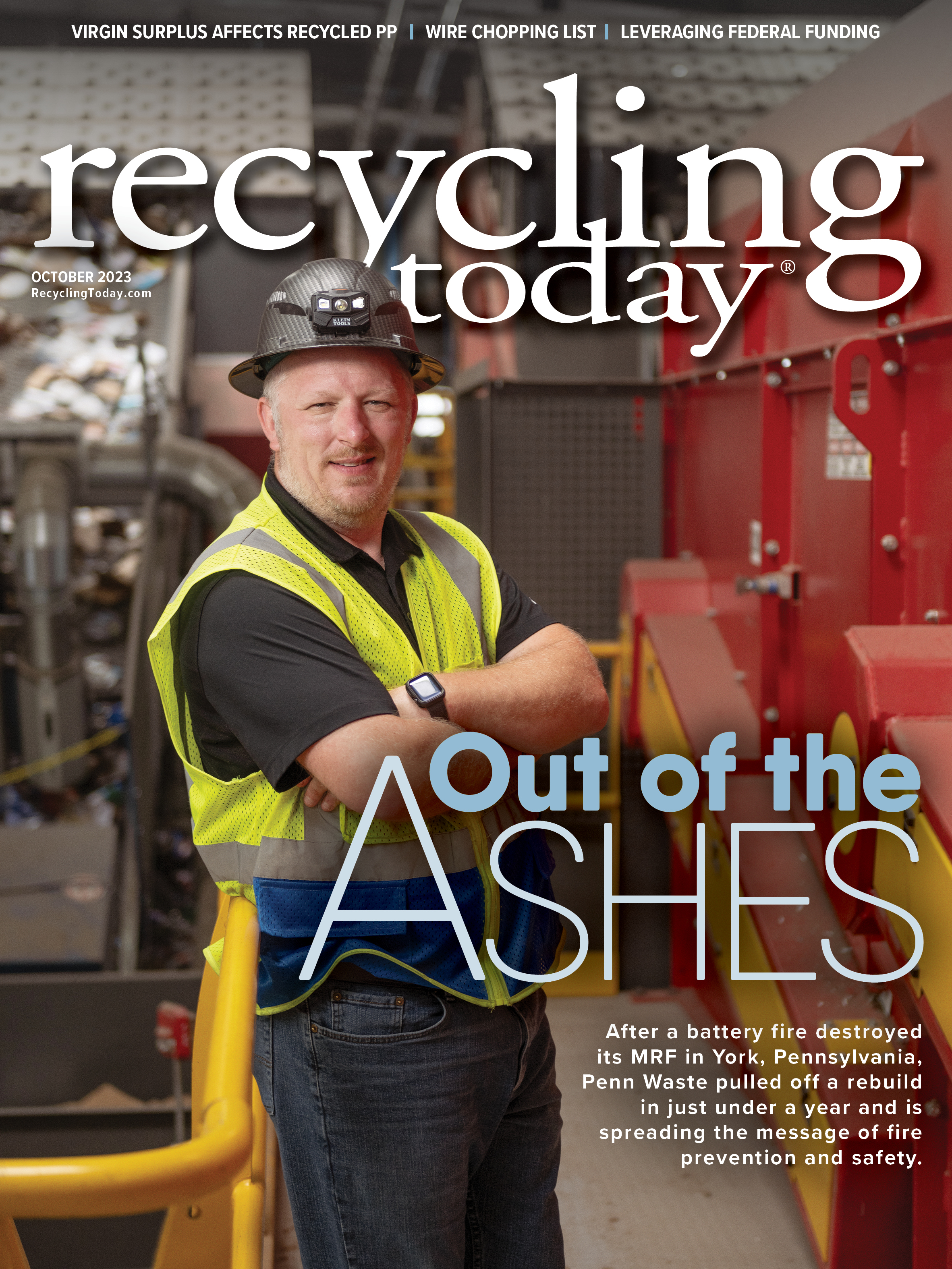
Explore the October 2023 Issue
Check out more from this issue and find you next story to read.