
Photo courtesy of Orbia
Plastic is one of the world’s most ubiquitous materials, essential to daily life as we know it. Production is growing at a rate of 3.4 percent—three times faster than our global population growth. However, recycling efforts have failed to keep up. They’ve been a patchwork solution at best and ineffective at worst, driving public distrust and skepticism.
Many of the challenges associated with plastic recycling can be attributed to single-use plastic, which typically is lightweight, contaminated and made from mixed resins—factors that make collection, sorting and processing technically difficult. When paired with a lack of standardized infrastructure, this often is economically unviable.
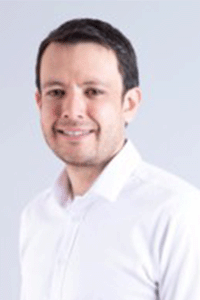
At the same time, polyvinyl chloride (PVC) recycling has emerged as a success story with relatively high recycling rates and the ability to be recycled up to seven times. PVC typically is found in long-life products like pipes, window frames, medical devices and flooring—products that usually are made from a single type of plastic and in settings that allow for controlled collection such as hospitals and construction sites.
While PVC recycling is showing early promise, the industry is at a critical juncture. In 2024, PVC recycling rates in the United States failed to grow, remaining at 27 percent while rates in Europe were only slightly higher. In addition, Latin America has remained a notoriously difficult region to scale plastic recycling with rates at 4 percent.
To build on PVC’s early promise, the industry now must pursue deliberate action to improve recycling rates to restore public trust and demonstrate a true commitment to contributing to the circular economy.
The Vinyl in Motion success story
One example of how PVC recycling can scale is through the Vinyl in Motion program, launched by Orbia’s Polymer Solutions business, Vestolit. The initiative was developed with the goal of closing the loop on PVC products, focusing on developing a value chain in Latin American sectors where clean, source-separated collection is possible.
The program started in Colombia in 2020 through collaboration with Baxter following a desire to use more sustainable materials. Orbia partnered directly with hospitals and patients to collect postconsumer PVC medical materials, such as IV bags, as well as with local recyclers to collect other PVC scrap. After collection, these materials are carefully separated from any other plastics (as PVC has a different melting point and cannot be mixed), broken down into scrap materials and finally reprocessed into pellets or new products such as pipes, floor mats and shoes.
Today, the program collects 150 tons of PVC scrap each month and expects to double its capacity throughout this year. In Colombia, Vinyl in Motion plans to reach 90 percent of the country's 2,500 healthcare facilities in the next five years as well as expand the program to Mexico and Brazil.
Vinyl in Motion has demonstrated that PVC recycling can succeed when the right conditions are in place, and has identified three critical components that are essential to scale recycling programs: perception shifts, quality control and value chain buy-in.
Changing PVC recycling perceptions
Despite its potential, PVC continues to face outdated misconceptions about both its safety and the value of recycled materials. Recycled plastics historically have been viewed as lower quality than virgin materials or merely as “filler,” causing customer hesitancy. For PVC, these doubts are compounded by legacy concerns about health and environmental impacts tied to production practices from decades past.
Today, those concerns no longer reflect reality: manufacturers of vinyl chloride adhere to some of the most stringent safety and environmental regulations in the chemical industry while pure PVC is inert and nontoxic. Moreover, Orbia has focused on developing premium quality recycled PVC, investing in specialized PVC mechanical recycling equipment to ensure it can stand up to the highest standards.
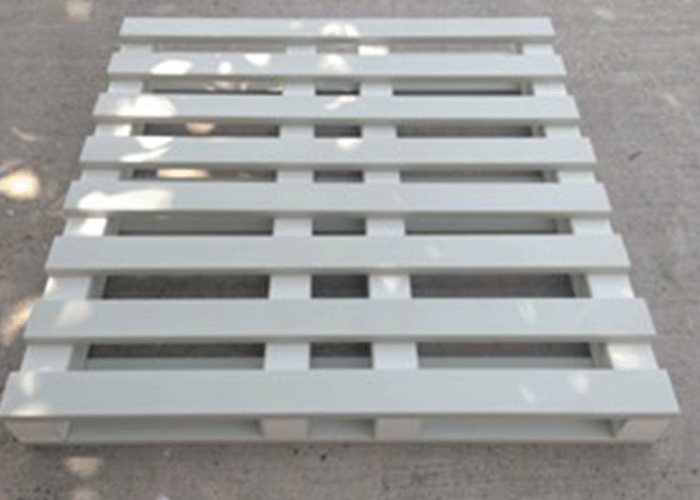
Educating customers, end users and consumers on the quality of recycled PVC and how it can be used in various products to lower carbon footprints is key to shifting perceptions. Orbia hosts workshops with stakeholders across the entire supply chain and supports customers with the materials they need to educate their end users to build demand. Once the value is clear, customers are willing to pay a premium, sending a clear signal that the market values responsible material sourcing and is ready to reward circular innovation.
Creating premium quality
Creating high-performing PVC starts at the source: training hospitals, construction sites and recyclers to properly separate and handle PVC, ensuring it remains clean and suitable for mechanical recycling.
Orbia launched the program in Colombia, where more than 10,000 patients receive home dialysis. Today, Orbia has trained and set up collection processes with more than 600 patients, preventing their PVC medical scrap from ending up in landfills or being discarded into the environment.
In addition, Orbia identified waste pickers on the street to train in PVC recycling, providing equipment, grants and educational opportunities to allow them to build individual recycling businesses to support the program and transform their quality of life.
On the technical side, Orbia has invested in equipment and developing processes with the recyclers produce recycled PVC that meets strict performance and safety standards. Orbia then purchases the scrap back from the recyclers and sends samples to prospective customers to allow them to run trials with the materials and determine how to integrate it into their products. In addition, the team provides training on how to mix scrap with virgin material for new applications or produce high-quality applications such as pallets and car mats with 100 percent recycled PVC. Orbia also produces its own compound from these materials, called Infinitude, which now is used by a variety of customers.
The premium cost of recycled PVC doesn’t just reflect quality; it reflects a story. A story of materials kept out of landfills, of life-changing job opportunities in local communities and of the shared value that’s created when quality and impact go hand-in-hand.
Gaining participation of the whole value chain
Since PVC often is found in long-life applications, it doesn’t flow through recycling systems at the same frequency as single-use materials such as packaging or plastic water bottles, making consistent volume a challenge. But that also presents an opportunity: there is room to design the full value chain intentionally, from collection to transformation.
Orbia, for example, has taken a collaborative, systemic approach to building out the Vinyl in Motion program. When producers, processors, distributors and end users are aligned, the entire system benefits. With Baxter, for instance, the collaboration started with a customer request and evolved into a closed-loop system that now informs how other hospitals and manufacturers are brought into the program. More partners mean more predictable volume, and with it, more financial viability. Scaling PVC recycling depends on that collective participation—not just from recyclers, but from every link in the chain.
The Vinyl in Motion program and its recent expansion to new countries has shown that successful PVC recycling is not only possible; it’s replicable. When approached as a system, with buy-in from the entire plastic production chain, PVC recycling offers a scalable, circular solution that can be a model for how the plastics industry can do better—by design.
Javier Pérez is the sustainability leader for Orbia’s Polymer Solutions business group, Vestolit. Based in Colombia, he has been with Orbia for more than six years, where he leads efforts to advance circularity, reduce emissions and embed sustainable practices throughout the value chain. Orbia's Polymer Solutions business group supplies the company’s downstream businesses and a global customer base with PVC general resins, specialty resins, compounds, derivatives and additives for vinyl compounds.
More from our latest newsletter
- Clean Vision breaks ground on West Virginia pyrolysis facility
- Otsego ReUse Center partners with NexTrex to tackle plastic waste
- McKinsey identifies engineering polymers as a recycling opportunity
- Amcor to expand PCR capabilities in Kentucky
- Second chemical recycling unit operational at ExxonMobil’s Baytown, Texas, facility
- CAA submits amended plan in Colorado
- EPR program launches in Oregon
- Malaysia to set stricter plastic import controls
- Reconomy launches Textile EPR Impact Assessment