
Photo courtesy of Starlinger
Portuguese plastics recycling company Ambiente S.A. is producing deodorized regranulate from washed agricultural films and detergent bottles with the help of a recoSTAR Dynamic 165 C-VAC recycling line from Vienna-based Starlinger.
The Starlinger line began operation this June in Ambiente’s new factory in Leiria, north of Lisbon, where the company recycles industrial and postconsumer plastic, including low-density polyethylene (LDPE) agricultural films and high-density polyethylene (HDPE) detergent bottles into pellets for film extrusion and blow molding applications.
Ambiente’s roots reach back to 1953, when its parent company, plastic film production company Fabrica Leiriense de Plasticos, was recycling its internal production scrap. From the early 1970s on, Fabrica Leiriense de Plasticos also processed externally collected plastic, including imported materials from other European countries, before becoming Portugal’s recycling pioneer for domestic plastic in the 1990s.
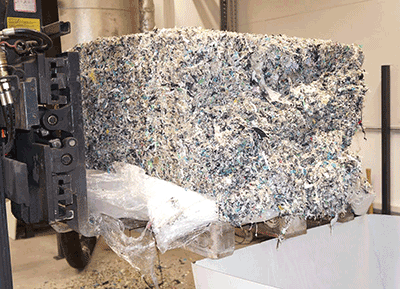
The company management’s awareness that plastics recycling constitutes a fundamental prerequisite for a sustainable future led to the foundation of Ambiente S.A. in 1989.
Ambiente became independent in 2000 and employs 36 people, recycling 7,000 tons of plastic per year. The recycled LDPE and HDPE pelletsit produces are supplied to customers throughout Europe and Northern Africa.
Odor-improved recycled pellets
The recoSTAR Dynamic 165 C-VAC recycling line installed at Ambiente features Starlinger’s odor reduction technology and processes HDPE detergent bottles washed postconsumer LDPE agricultural films.
“Agricultural films are used for various applications—for example in greenhouses, as crop covering or for silage,” says Paul Niedl, commercial head of Starlinger Recycling Technology. “This results in organic residues being present even after washing, which create gases in the subsequent recycling process.”
Niedl says with the detergent bottles, the scent of the detergent migrates into the packaging material over the course of its storage and use. “Our odor reduction technology is designed to permanently remove such odors so that the produced regranulate is suitable for high-level applications. Instead of downcycling, it can be reused in the same application, which creates circularity.”
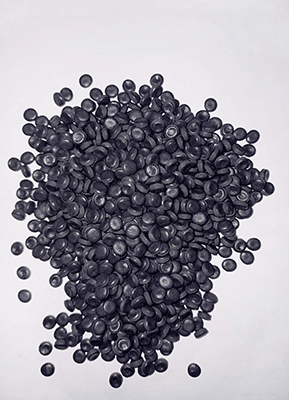
Starlinger says the recycling process can be adapted according to the contamination and odor intensity of the input material and the desired specifications of the regranulate.
The process starts with cutting and homogenizing the input material in the SMART feeder, where the material is heated until it reaches the ideal temperature. Highly volatile odors are extracted during this step. After the main extruder, the melt passes through continuous melt filters, which remove solid contaminants so they cannot release odors during the following process steps, according to the company. In the subsequent C-VAC module, the melt surface is increased by 300 percent, achieving extremely high degassing efficiency and ensuring that even deeply embedded odors are permanently extracted.
Sponsored Content
SENNEBOGEN 340G telehandler improves the view in Macon County, NC
An elevated cab is one of several features improving operational efficiency at the Macon County Solid Waste Management agency in North Carolina. When it comes to waste management, efficiency, safety and reliability are priorities driving decisions from day one, according to staff members of the Macon County Solid Waste Management Department in western North Carolina. The agency operates a recycling plant in a facility originally designed to bale incoming materials. More recently, the building has undergone significant transformations centered around one machine: a SENNEBOGEN telehandler (telescopic handler).
In the final step, the recycled pellets are treated in the pellet conditioning unit to extract the most persistent odors. This ensures permanently odor-improved regranulate that can be used for manufacturing a wide range of plastic products, Starlinger says.
Get curated news on YOUR industry.
Enter your email to receive our newsletters.
Latest from Recycling Today
- LME reports active Q2
- Liberty Steel assets facing financing deadlines
- Sims is part of Australian recycling loop
- Tariffs target steel exporters Brazil, Canada and South Korea
- Buy Scrap Software to showcase its software at Scrap Expo in September
- LG details recycling activities
- Algoma EAF is up and running
- Toyota-Tsusho completes acquisition of Radius Recycling