
Photo courtesy of ADEM/Direct Communications
More than 5 million tires are replaced and scrapped every year in Alabama. When improperly discarded, old tires can be an environmental menace.
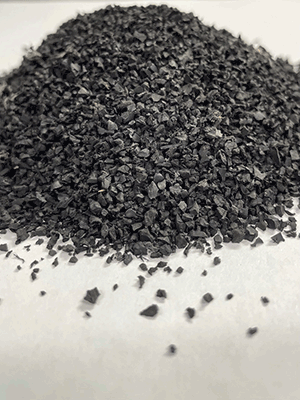
Photo courtesy of ADEM/Direct Communications
Using crumb rubber to offset inject carbon
at rates ranging from 5-30 percent would
consume approximately 350 to 2,100 tons
of scrap tire materials annually.
It is not uncommon to see scrap tires abandoned along roadsides, littered in rivers, creeks and other streams and strewn across the countryside. There, they are eyesores and impair natural resources. They also often are piled in illegal tire dumpsites, where they are fire hazards and accumulate water to become breeding grounds for mosquitoes and other pests.
Even when properly disposed, scrap tires still can be a problem. They take up valuable space in landfills, and sometimes after being buried, tires can work themselves back to the surface and require follow-up cleanup.
To combat these problems, the Alabama Department of Environmental Management (ADEM) has invested tens of millions of dollars over the past two decades to assist local communities in cleaning up improperly discarded tires and to promote innovative and beneficial uses for scrap tires so fewer would be thrown away.
As ADEM is seeking ways to solve the scrap tire problem, steelmaker SSAB Alabama Inc. is looking for opportunities to make its steelmaking more environmentally friendly. Last year, SSAB completed a trial project in collaboration with ADEM that promises to help the regulatory agency and the steelmaker accomplish their individual goals.
SSAB, which operates a twin-shell AC electric arc furnace (EAF) melt shop in Axis, Alabama, near Mobile, undertook an ADEM-funded trial project to test the viability of using crumb rubber from scrap tires in its steelmaking process. The purpose of the project was to determine whether the recycled tires practically and effectively could replace some of the pet coke, or petroleum coke, used in steel production.
The benefit for SSAB would be a safe and environmentally responsible alternative carbon source to traditional coke, which is derived from oil refining. For ADEM, the project would demonstrate another practical use for recycled scrap tires.
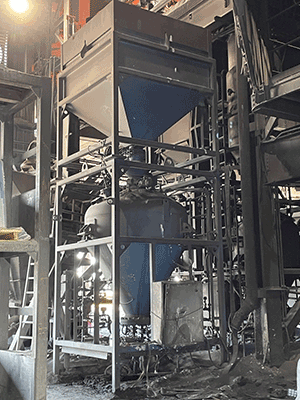
During the trial project, SSAB substituted the crumb rubber for some of the pet coke, a traditional ingredient used in steelmaking, while measuring its performance and assessing the impact on emissions and operations.
SSAB officials were pleased with the results. “Steel quality was not impacted in any negative way, and the furnace efficiency performed suitably,” SSAB metallurgical engineers write in the company’s final report on the project.
ADEM officials also were excited about the trial project’s findings.
“Any time you can take a scrap or waste product, such as old, discarded tires, and identify a productive and commercially viable use for it, that’s very encouraging,” says Stephen Cobb, head of the Land Division at ADEM. “It both solves a problem—what to do with scrap tires that are costly to dispose and can have a detrimental effect if not disposed of properly—and creates a marketable and productive use for the tires that benefits the environment. ADEM loves these types of projects, and we are grateful the Alabama Legislature recognized that scrap tires were a growing concern and enacted a law with a funding source to find better solutions.”
In 2003, the Alabama Legislature passed the Alabama Scrap Tire Environmental Quality Act to ensure the proper disposal of scrap tires. To fund the effort, lawmakers included a $1 fee on each tire bought or replaced in the state. Using that money, ADEM created the Scrap Tire Program to pay for cleaning up tire dumps and tires littered along roadsides and elsewhere.
In addition, ADEM awards grants from the fund to incentivize trial projects that use scrap tires, such as paving roads and parking areas with rubber-modified asphalt and surfacing playground and walking areas with shredded tire materials. It also included funding for SSAB to test crumb rubber in steelmaking.
For its injection carbon optimization trial, SSAB was awarded a $361,000 grant from ADEM in December 2021. The money was used to purchase the crumb rubber and specialized equipment to inject the material into the EAF. Liberty Tire Recycling, headquartered in Pittsburgh, provided the crumb rubber from recycled tires, and a third-party engineering company, Gas Cleaning Technologies (GCT), Irving, Texas, was employed to assist with testing and assessing any impact on gas emissions.
SSAB injected crumb rubber in various concentrations into the plant’s West Furnace. The trials were performed using substitutions of crumb rubber for coke in increments of 5 percent ranging from 5-30 percent. SSAB ran a total of 51 trial heats.
During each trial, slag samples were taken to observe conditions and anomalies. SSAB also looked for potential risks and problems with the crumb rubber injection, such as higher emissions and slag foaming, inefficient carbon slag forming, higher electrode consumption, refractory wear and high nitrogen content in the steel. The steel was monitored to avoid nonconforming customer products.
EAF Furnace off-gasses were monitored using a specialized probe installed in the direct evacuation control duct upstream of the tie-in with the main duct to the EAF baghouse. Oxygen (O2), carbon monoxide (CO), carbon dioxide (CO2), sulfur dioxide (SO2) and nitrogen oxide (NOx) levels were measured.
“As far as steel quality is concerned, there were no visible concerns seen with the chemistry of the final product,” according to the SSAB report. “Customer satisfaction was met with specifications fulfilled both internally and externally. Slag conditions were favorable while utilizing the crumb rubber material. The viscosity was ‘creamy’ in appearance, indicating an increase in overall yield, requiring less overall flux consumption and maintaining refractory integrity in the furnace.”
On the air emissions testing, the report says GCT did not note “any off-gas conditions that would hinder production, lead to a safety concern or lead to higher environmental emissions. Average emissions seemed environmentally acceptable, and no major variations were detected between scrap tire crumb rubber heats and base-line heats using conventional carbon. Based on the data available to date and trials conducted, GCT believes crumb rubber to be a suitable alternative to conventional carbon when looking at gas emissions.
“To summarize the trial results: There were no detrimental findings observed with utilizing the crumb rubber material at SSAB. Steel quality was not impacted in any negative way, and the furnace efficiency performed suitably.”
SSAB uses approximately 7,000 tons annually of inject carbon (pet coke) and another 25,000 tons of charge carbon in its EAF steelmaking process. Using crumb rubber to offset inject carbon at rates ranging from 5-30 percent would consume approximately 350 to 2,100 tons of scrap tire materials annually. As EAF processes vary, SSAB says crumb rubber potentially could offset charge carbon as well.
SSAB says it is looking for opportunities to expand its use of recycled tire materials to make its steelmaking operations more environmentally sustainable. ADEM, the state environmental regulatory agency, says it would love to see that and the development of a supply line for crumb rubber from discarded tires for ready use in steelmaking.
“This has the potential of greatly adding to the marketability of recycled tires, making scrap tires more than just throw-aways,” Cobb says. “If consumers and tire shops know that their scraps have value, they would take more care in their disposal. In essence, throwing away scrap tires could literally be throwing away money. That would be great news for the environment.”
Eddie Lard contributed this article on behalf of the Alabama Department of Environmental Management.
Get curated news on YOUR industry.
Enter your email to receive our newsletters.
Latest from Recycling Today
- Coperion, Herbold bringing plastic recycling technologies to K Show
- Schupan and Sons appoints VP of Human Resources
- Vanden launches catalogue for recycled PET resins, flake
- PCA: Corrugated products customers ‘cautious’ amid economic uncertainty
- McKinsey sees recycling as an aluminum supply necessity
- RegenX delays annual report, says it is nearing facility restart
- WM Kelley moves into new offices
- US Senate backs reduced cuts to EPA