
Photo courtesy of SSI Shredding Systems
With dwindling legal export markets for plastics generated from end-of-life electronics in the U.S., Houston-based CompuCycle has developed a shredding, cleaning and sorting system designed to produce materials that can be recycled domestically.
“Plastics [are] becoming what some people may consider a focused material,” CompuCycle President Clive Hess says.
The information technology (IT) asset management company’s electronics recycling plant features two four-shaft shredders, a Quad Q100 and a Quad Q70, made by SSI Shredding Systems Inc., based in Wilsonville, Oregon. This processing line breaks down end-of-life electronics into its individual components.
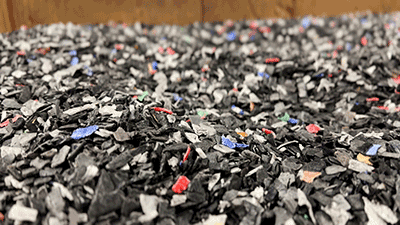
electronics that it can sell directly to OEMs.
More than 50 million tons of end-of-life electronics are generated annually worldwide, 20 percent of which contain plastics. These complex materials often contain hazardous substances such as brominated flame retardants and heavy metals. This not only makes them a challenge to recycle but also poses a significant risk to the environment and human health if not managed properly.
“That's why I truly do call it the 'wow machine,' because to see it from going up one conveyor belt and then turning into this next piece of material of really raw components of that steel, plastic, aluminum, copper and boards, it's just amazing,” CompuCycle CEO Kelly Adels Hess says.
“CompuCycle wanted a shredder versatile enough to handle bulk-fed loads of e-plastics originating from any processor out there. Our SR500 Uni-Shear can hold up to 4 cubic yards of volume and make small, well-liberated output size, so it’s perfectly suited for this task,” says Dave Fleming, vice president of sales and marketing at SSI.
In November 2023, CompuCycle started up its e-plastics processing plant, which features a single-shaft Uni-Shear SR500 shredder and sink-float tanks that can separate e-plastics into their base components, such as polyethylene, polypropylene, polystyrene and acrylonitrile butadiene styrene plastics.
“With being able to clean these plastics and to be able to separate these plastics, we can go now directly to [original equipment manufacturers],” Adels Hess says.
Sponsored Content
SENNEBOGEN 340G telehandler improves the view in Macon County, NC
An elevated cab is one of several features improving operational efficiency at the Macon County Solid Waste Management agency in North Carolina. When it comes to waste management, efficiency, safety and reliability are priorities driving decisions from day one, according to staff members of the Macon County Solid Waste Management Department in western North Carolina. The agency operates a recycling plant in a facility originally designed to bale incoming materials. More recently, the building has undergone significant transformations centered around one machine: a SENNEBOGEN telehandler (telescopic handler).
Sponsored Content
SENNEBOGEN 340G telehandler improves the view in Macon County, NC
An elevated cab is one of several features improving operational efficiency at the Macon County Solid Waste Management agency in North Carolina. When it comes to waste management, efficiency, safety and reliability are priorities driving decisions from day one, according to staff members of the Macon County Solid Waste Management Department in western North Carolina. The agency operates a recycling plant in a facility originally designed to bale incoming materials. More recently, the building has undergone significant transformations centered around one machine: a SENNEBOGEN telehandler (telescopic handler).
Sponsored Content
SENNEBOGEN 340G telehandler improves the view in Macon County, NC
An elevated cab is one of several features improving operational efficiency at the Macon County Solid Waste Management agency in North Carolina. When it comes to waste management, efficiency, safety and reliability are priorities driving decisions from day one, according to staff members of the Macon County Solid Waste Management Department in western North Carolina. The agency operates a recycling plant in a facility originally designed to bale incoming materials. More recently, the building has undergone significant transformations centered around one machine: a SENNEBOGEN telehandler (telescopic handler).
Get curated news on YOUR industry.
Enter your email to receive our newsletters.
Latest from Recycling Today
- Algoma EAF is up and running
- Toyota-Tsusho completes acquisition of Radius Recycling
- CATL, Ellen MacArthur Foundation aim to accelerate circular battery economy
- Commentary: Expanded polystyrene: 98 percent air, 2 percent plastic, 100 percent misunderstood
- AMCS appoints general manager for North America
- How tariffs, regulations affect LIBs recycling in US, EU
- Schwan Cosmetics introduces packaging free of styrene, ABS
- Aimplas coordinates EU project focused on solar panel circularity