
Photo by DeAnne Toto
Amazon claims four guiding principles: customer obsession rather than competitor focus, passion for invention, commitment to operational excellence and long-term thinking. Through the company’s focus on waste diversion in its operations, transitioning away from single-use plastics to paper in itsdelivery packaging where possible and developing biobased plastics that can be recycled or composted when using plastics is unavoidable, Amazon is acting on these principles while also working toward its commitment to reach net-zero carbon emissions across its global operations by 2040 as part of its 2019 co-founding of The Climate Pledge with Global Optimism.
To minimize waste across its operations, which includes everything from the infrastructure used in its operations to the products sold online and in its grocery stores, the company uses data to identify the highest-impact opportunities. It then follows a three-step approach to minimize waste that involves prevention, reduction and reuse. For the waste that cannot be avoided, recycling and composting are prioritized over energy recovery, with waste treatment and disposal representing the least favored disposal option.
While that framework might sound simple, Amazon says significant effort and innovation are needed to create practical, scalable solutions across its various businesses and thousands of sites.
Inside its operations
Through its sustainability efforts in 2024, Amazon diverted 85 percent of the waste generated in its internal operations from landfill, an incremental improvement from the 84 percent rate it achieved in 2023 and 3 percentage points more than the 82 percent rate achieved in 2022. Of that 85 percent, Amazon says 83 percent was recycled or composted, while 2 percent of the company’s waste was incinerated with energy recovery last year.
Cardboard, or old corrugated containers (OCC), and wood make up 65 percent of Amazon’s waste footprint, and they are nearly 100 percent recycled, according to the company.
Justine Mahler, director, technical product management, waste, water and biodiversity, at Amazon, tells Recycling Today that the variety of items Amazon handles and its global scale make waste management complex and challenging, adding that Amazon relies on strong partnerships to realize its goals.
She says Amazon works with more than 350 service providers on recycling solutions across its operations for items that include personal protective equipment (PPE), pallets, stretch wrap and industrial equipment used in its fulfillment centers.
Jill Philips Ortega, general manager of Amazon’s BFI3 fulfillment center in DuPont, Washington, roughly 50 miles south of the company’s corporate headquarters in Seattle, says even safety shoes generated at BFI3 and other sites are recycled or reused through Soles4Souls, a nonprofit with U.S. operations based in Tennessee.
Mahler says where and how recycling solutions are implemented in Amazon’s operations are critical to their success, noting the placement of the PPE recycling station next to the employee exit during a late June site visit. Amazon works with New Jersey-based TerraCycle to recycle the high-visibility vests and gloves its associates generate at BFI3 and other sites.
New material recycling mechanisms must fit in as seamlessly as possible given the scale and speed of Amazon’s operations. (For example, the company delivered at its fastest speeds ever for Prime members globally in 2024, with more than 9 billion items delivered the same or next day.)
In its fulfillment centers, Amazon uses color-coded bins to capture OCC and stretch wrap generated by its operations, baling these materials on-site.
Amazon also recycled 16 percent more of its label backing in 2024 in North America, Mahler says. Amazon achieved this in collaboration with RafCycle by UPM Raflatac, which produces building insulation and coffee cups using the material. In Japan, Amazon works with a vendor to recycle this material into toilet paper, increasing recycling by 50 percent from 2023 to 2024. Despite these successes, the company is exploring how to eliminate label backing eventually, Mahler says.
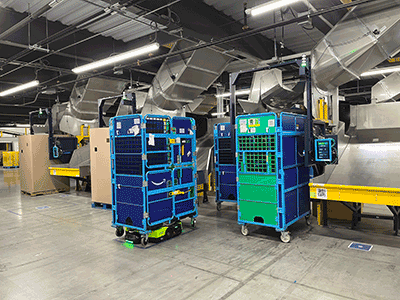
wood pallets across its fulfillment centers in 2024.
By using what it calls GoCarts, or reusable wheeled carts, to transport outgoing packages in its trucks, Amazon avoided 85 million disposable wood pallets last year across its fulfillment centers, Philips Ortega says, as well as the emissions related to operating forklifts to handle the pallets.
The company is leveraging reuse in other areas of its operations, including developing mechanisms that connect unused assets across its sites to another site or to charities. These mechanisms allowed Amazon to repurpose 310,000 assets and materials from these programs in 2024. For example, in Valencia, Spain, 5,000 unused assets that included first aid supplies and shelving were donated to Fundación Altius to support disaster relief efforts and affected communities following the floods, according to Amazon.
Amazon’s logistics network enables the company to move quickly when assisting in disaster recovery efforts.
Before removing overstock from its inventory, Amazon tries to sell it at a discount through Amazon Outlet, while Whole Foods Market works with Too Good To Go, an app that enables customers to purchase surplus food at discounted prices. In 2024, the company sold 68 million retail sellers’ items via Amazon Outlet and diverted the equivalent of 636,000 meals through Too Good To Go in the U.S.
Additionally, Amazon MGM Studios launched its first Reusable Asset Hub in North America in 2024, which houses production items ranging from electronics to furniture that can be reused for future Amazon productions. Nearly 15 productions have benefited from this resource, including Countdown, Criminal and Buy It Now, Amazon says.
Amazon also has introduced online shopping features, including artificial intelligence- (AI-) generated customer review summaries. “Frequently returned item” and “Customers usually keep this item” badges and clothing size recommendations help customers make more informed purchasing decisions, which can help reduce returns.
Addressing damaged products
While Amazon reduced the percentage of damaged items within its operations by 29 percent last year compared with 2023, goods are still damaged in transit and handling.
Amazon associates work to identify damage early in the process, Mahler says, evaluating whether it’s a cosmetic packaging issue or damage to the actual product that will affect its appearance and function.
Philips Ortega adds that the company collaborates with its vendors to reduce damage to items.
When possible, Amazon says it sends damaged products for repair to enable resale. Its top repair categories in 2024 included laptops, tablets, robotic vacuums and espresso machines.
Also in 2024, Amazon donated the equivalent of 81 million meals globally—60 million in the U.S. and 21 million in Europe. The company recently collaborated with Chicago-based Feeding America to expand its ability to donate food products from its operations to food banks, food pantries and local food programs across the Feeding America network.
Amazon leverages its team members’ relationships with local schools and nonprofits to facilitate local donations, Philips Ortega says.
“Our most passionate employees work in the donation area,” Mahler adds.
Amazon says it continues to find ways to prevent, reduce, reuse and recycle or compost, innovating where solutions don’t currently exist. One example of this is the bioplastic solutions the company is helping develop in its Sustainable Materials Innovation Lab.
Innovating biobased plastics
When it comes to the packaging materials used at Amazon, the company has prioritized the use of curbside recyclable materials, which has led to its phaseout of plastic in favor of paper-based packaging whenever possible.
However, not all plastic can be eliminated, particularly when it comes to food packaging.
That fact led Amazon to join the BOTTLE (Bio-Optimized Technologies to keep Thermoplastics out of Landfills and the Environment) Consortium, led by the Department of Energy’s National Renewable Energy Laboratory (NREL).
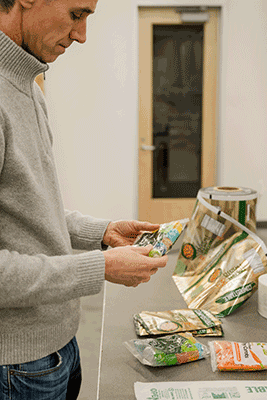
packaging at Amazon's Sustainable
Materials Innovation Lab in Seattle.
Through this consortium, Amazon has helped develop what Alan Jacobsen, director of materials and energy sciences at Amazon, describes in a March 2022 Amazon Science article as “an energy-efficient chemical processing technology that can break down or deconstruct a mixed waste stream of plastics with labile bonds (i.e., bonds that are easy to deconstruct) into valuable feedstock that can be used to make the same types of plastics (closed-loop recycling) or new plastics altogether (open-loop recycling). And in the cases where these materials don’t make it into a future recycling stream, the molecular structure of these materials can be designed to biodegrade in natural environments.”
In a late June visit to his lab, Jacobsen tells Recycling Today that Amazon, its grocery stores and its partners, which include material scientists, a recycling technology startup and biomaterials producers, are demonstrating how to prove out a new value chain for plastics derived from renewable resources that are easily recycled while also being biodegradable.
Jacobsen says the team focused on polyester-based biodegradable plastics, which contain carbon-oxygen ester bonds that are easier to break down than the carbon-carbon bonds found in polyolefins, such as polyethylene or polypropylene. He adds that solvolysis techniques, such as methanolysis and glycolysis, being developed for polyethylene terephthalate (PET) could be extended to other polyesters, such as polylactic acid (PLA) or polyhydroxyalkanoates (PHAs), that are more readily biodegradable.
PLAs and PHA commonly are made using renewable, organic sources, such as corn starch or sugar cane, but Jacobsen says the BOTTLE Consortium is looking into using second-generation feedstocks, such as ag waste and cellulosic biomass, for their production.
While Amazon’s work with NREL is targeting flexible films because they present the biggest challenge to recycle today, having a separate recycling stream for each new type of biopolyester plastic would not be practical nor economical, Jacobsen says, nor would it solve the problem of recycling blends and multilayered materials.
PLA is a contaminant in the PET recycling stream currently, and its compostability is related to its form factor, with film breaking down more easily than rigid packaging, he says.
However, if this material and other biopolyesters were collected with PET thermoformed containers, they could be chemically recycled using methanolysis, which, he says, “can transform the carbon we have into the carbon we want.”
The consortium led to the establishment of EsterCycle, a Golden, Colorado-based startup founded by one of the BOTTLE Consortium collaborators at NREL, Julia Curley. That company has developed technology that uses low-energy methanolysis processes with an amine catalyst to selectively break the ester bonds that form these polymers.
For EsterCycle to be able to commercialize its technology, however, a reliable supply of materials to process is needed. Amazon called on its partnership with San Francisco-based Glacier to assist in this area.
Glacier, which Amazon’s Climate Pledge Fund invested in last year, uses AI-powered robots to sort recyclables and collect real-time data on recycling streams. The companies launched a trial at a material recovery facility (MRF) in San Francisco to test how effectively Glacier’s AI vision and robotic systems could identify and sort biopolyester packaging, learning that packaging design significantly influences AI detection. Glacier’s AI identified packaging with consistent, visible features 99 percent of the time, Jacobsen says, though lookalike materials and inconsistent designs led to higher rates of misidentification.
Amazon also is testing and trialing these biopolyesters in real-world applications, including in produce bags made with Italy-based Novamont's Mater-Bi material in Amazon Fresh stores in Seattle, while shelf-life testing shows the bags perform similarly to conventional plastic bags in keeping produce fresh for the first week after purchase. Different types of produce showed varying results in longer-term storage, however, which Amazon is working with materials developers to improve, Jacobsen says.
Other innovations
Other Amazon packaging innovations have focused on more traditional packaging materials and waste reduction designed to improve the customer experience.
Innovations are tested at Amazon’s BF1 fulfillment center before being deployed more widely, with the sites’ associates providing feedback. Deployability is taken into account with new innovations, says Josh Samples, senior manager and global field lead for Mechatronics & Sustainable Packaging at Amazon.
“We’re here to accelerate ideas,” he says of his team. “Sometimes that’s into the ground.”
John Sly, senior manager, Mechatronics & Sustainable Packaging, adds that failing early in the development process is preferable.
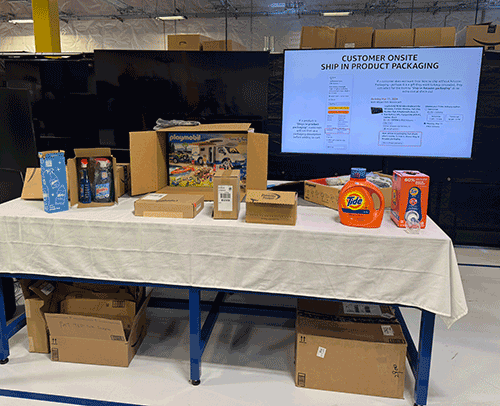
Amazon introduced its Ships in Product Packaging (SIPP) program (formerly Ships in Own Container) in 2015 for its first-party products. As of 2024, the company expanded SIPP to all sellers using Fulfilled by Amazon (FBA), giving them the opportunity to test and qualify products to ship to customers in their brand packaging without any Amazon-added material. The testing subjects the packaging to 17 different drop tests, Samples says.
The company says SIPP provides a better customer experience by minimizing the packaging materials used for delivery while also reducing the costs associated with fulfillment and potentially lowering the carbon footprint of outbound shipments.
Sly says 12 percent of Amazon’s shipments in 2024 were SIPP.
The company’s transition away from plastic bubble mailers to paper-based mailers began in 2019, with the introduction of the paper padded mailer. In 2023, Amazon’s Euclid, Ohio, fulfillment center, outside of Cleveland, became the first facility to convert to solely paper-based packaging. Machines scan items to create a mailer that is the right size for the shipment, reducing air and using less packaging.
However, associates found that their hands fatigued more easily working with the paper mailers, which led Amazon to make minor changes to the packaging to make it easier to work with, Samples says.
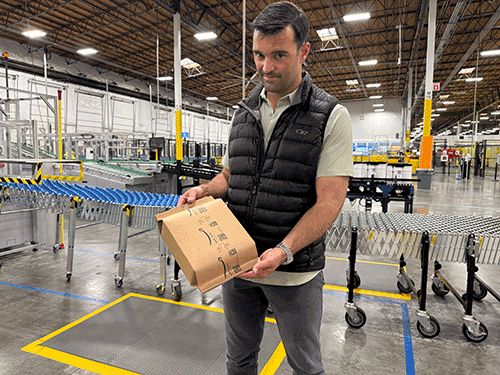
company's BFI1 fulfillment center outside Seattle.
Amazon began introducing a new version of its right-sized cardboard box technology in 2024. Sly says the packaging material removes one layer of liner from the corrugated medium, reducing weight. Sensors on the machine measure the dimensions of the item being shipped to create a custom box on-site.
He says the technology is used to ship items that require more protection than a padded paper mailer can provide.
At its manual packaging stations, Amazon provides associates with suggestions for how to package orders, but Samples says associates have the ultimate say on how items are shipped. They are encouraged to give Amazon feedback to optimize its packaging further.
Whether reducing and recycling its internal waste or ensuring the packaging its customers receive is more readily recyclable, Amazon plans to continue to take steps to reduce the environmental footprint of its packaging and operations.
Sponsored Content
SENNEBOGEN 340G telehandler improves the view in Macon County, NC
An elevated cab is one of several features improving operational efficiency at the Macon County Solid Waste Management agency in North Carolina. When it comes to waste management, efficiency, safety and reliability are priorities driving decisions from day one, according to staff members of the Macon County Solid Waste Management Department in western North Carolina. The agency operates a recycling plant in a facility originally designed to bale incoming materials. More recently, the building has undergone significant transformations centered around one machine: a SENNEBOGEN telehandler (telescopic handler).
Sponsored Content
SENNEBOGEN 340G telehandler improves the view in Macon County, NC
An elevated cab is one of several features improving operational efficiency at the Macon County Solid Waste Management agency in North Carolina. When it comes to waste management, efficiency, safety and reliability are priorities driving decisions from day one, according to staff members of the Macon County Solid Waste Management Department in western North Carolina. The agency operates a recycling plant in a facility originally designed to bale incoming materials. More recently, the building has undergone significant transformations centered around one machine: a SENNEBOGEN telehandler (telescopic handler).
Get curated news on YOUR industry.
Enter your email to receive our newsletters.
More from our latest newsletter
- Clean Vision breaks ground on West Virginia pyrolysis facility
- Otsego ReUse Center partners with NexTrex to tackle plastic waste
- McKinsey identifies engineering polymers as a recycling opportunity
- Amcor to expand PCR capabilities in Kentucky
- Second chemical recycling unit operational at ExxonMobil’s Baytown, Texas, facility
- CAA submits amended plan in Colorado
- EPR program launches in Oregon
- Malaysia to set stricter plastic import controls
- Reconomy launches Textile EPR Impact Assessment