
Image courtesy of 3form
For 25 years, 3form has sought to liven up professional spaces, such as offices and health care facilities, with a growing range of architectural resin panels in an array of colors, patterns and sizes.
And while designing plastic and glass panels for use as partitions, doors, shelving, acoustics, walls and more, the company, headquartered in Salt Lake City, has incorporated increasing amounts of recycled-content plastic into some of its signature products.
Mechanically recycled plastics have long been used in 3form products, but, in 2024 the addition of chemically recycled material allowed the company to take a leap forward and offer a line of panels made with 100 percent-recycled content.
All along, the company has attempted to merge circularity and creativity in its designs.
“Sustainability has always been a core value of 3form,” says Karli Slocum, the company’s vice president of product and marketing.
“We are looking at everything from our material and our hardware to our manufacturing processes to minimize waste and reduce carbon emissions. We have been working with various groups across the U.S. to figure out how to reclaim all materials when they have reached their end of life to be repurposed and, ideally, not a single 3form material would ever land in a landfill.”
According to Slocum, 3form has approximately 400 employees. In addition to its Salt Lake City headquarters—which also houses its main fabrication facility—the company has a glass factory in Kernersville, North Carolina, and its LightArt office in Seattle. The LightArt team designs lighting systems for 3form materials that are used in interior and exterior applications.
All 3form products are made in the U.S., and Slocum says the majority of the company’s supply chain for its leading materials, which include the Varia, 3form Glass and Koda XT lines, are sourced in the U.S.
Adding recycled content
3form first incorporated recycled-content plastic into its flagship Varia line in 2007, Slocum says, and now, each Varia panel includes 40 percent recycled content. Not long after, the company began to work on what became its Flek product line, which she says took more than 10 years of research and development to create its first 100 percent-recycled product.
“[Flek] uses internal scrap in the production of Varia, which is repurposed back into a panel, effectively decreasing a large amount of production waste,” Slocum says.
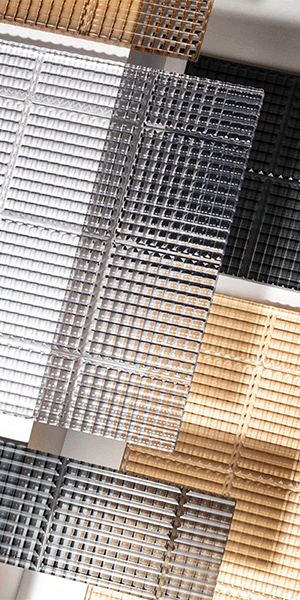
3form sources recycled materials from various suppliers that provide discarded, postconsumer and postindustrial plastics. Slocum says most of these materials are gathered globally to help support the company’s sustainability goals. As a result, the company’s 100-percent-recycled Textures line is comprised of 40 percent postindustrial plastic and 60 percent postconsumer plastic.
In addition to being a 100 percent-recycled line of panels, the Textures line stands out because the 60 percent of postconsumer plastic used comes from chemically recycled feedstock, which the company began sourcing in 2024. In particular, the plastic is processed using a methanolysis technology, which breaks down polyester into base molecules and enables the production of what Slocum describes as virgin-quality materials.
Methanolysis is a type of processing that can break down hard-to-recycle materials such as carpet fibers, textiles, packaging and colored plastics.
“Methanolysis focuses on material-to-material recycling,” she says. “We work with our U.S.-based suppliers to procure the right recycled material to achieve a high level of recycled content without sacrificing aesthetics. You can’t tell the difference between our 40 percent recycled material with 100 percent-recycled material, which was very important to our customers.”
Slocum notes several environmental benefits of 3form’s expansion into the use of mechanically and chemically recycled material. “One Varia Textures panel diverts an equivalent of 3,296 plastic water bottles from the landfill. One Varia panel diverts the equivalent of 1,318 plastic water bottles from the landfill. By using molecularly recycled material in our Varia panels, we can achieve a 25 percent reduction in manufacturing emissions compared to virgin material.”
She claims that for every 50,000 pounds of molecularly recycled material processed, 21,000 pounds of CO2 equivalent emissions are avoided.
“Molecular recycling has allowed us to make our entire Textures collection of Varia out of 100 percent-recycled material,” Slocum says.
“Our Varia line as a whole is made of 40 percent recycled material, and we hope to increase that number in the future. The key was advancement in molecular recycling technology and the ability to achieve a 100 percent-recycled product that is completely translucent. In the past, most recycled products were murky and more brittle. The new technology allows us to use plastic waste but still retain all of the characteristics our customers expect with Varia.”
Looking at the landscape
3form views the increased use of recycled materials as a “massive opportunity” in the architecture and design industry, Slocum says, adding that “more and more design firms are implementing sustainable requirements that manufacturers’ materials and products must meet to be specified on a project.”
Sponsored Content
Screen Smarter, Process Faster with GK’s FINGER-SCREEN FreeFlow™!
Upgrade to the next level of material separation with the FINER-SCREEN FreeFlow™ —built for efficiency, durability, and maximum throughput. With no bottom pan to clog, it handles bulky and wet materials effortlessly. Minimize jams, maximize uptime, and boost productivity. Optimize your operation today!
Sponsored Content
Screen Smarter, Process Faster with GK’s FINGER-SCREEN FreeFlow™!
Upgrade to the next level of material separation with the FINER-SCREEN FreeFlow™ —built for efficiency, durability, and maximum throughput. With no bottom pan to clog, it handles bulky and wet materials effortlessly. Minimize jams, maximize uptime, and boost productivity. Optimize your operation today!
Sponsored Content
Screen Smarter, Process Faster with GK’s FINGER-SCREEN FreeFlow™!
Upgrade to the next level of material separation with the FINER-SCREEN FreeFlow™ —built for efficiency, durability, and maximum throughput. With no bottom pan to clog, it handles bulky and wet materials effortlessly. Minimize jams, maximize uptime, and boost productivity. Optimize your operation today!
In her view, however, some significant challenges remain, such as collecting, sorting and transporting the proper materials to the proper location for recycling.
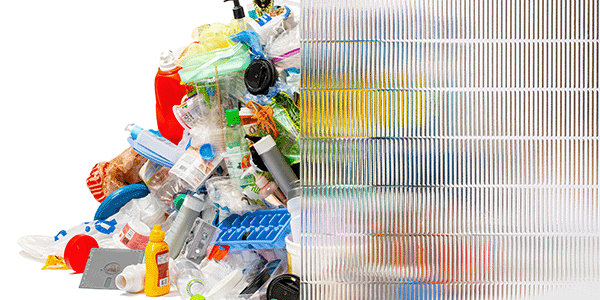
“This infrastructure is not prevalent across the U.S., and municipalities across the country have different approaches and processes when it comes to recycling,” she says. “For molecular recycling, specifically, we hope that more U.S. manufacturers will adopt this technology to make it more widely accessible and cost-effective.”
3form remains committed to sustainability within its own operations. For example, the company has offered its Reclaim program since 2005, where it accepts used panels and blemished sheets that otherwise could be landfilled.
“We carefully evaluate previously used panels for opportunities to rehome, reuse or recycle the materials,” Slocum says. “When customers undertake installation removals and connect with 3form, we facilitate local material rehoming where feasible, minimizing transportation impacts while extending product life.”
The company also has obtained a Just label, a transparency tool created by the Portland, Oregon-based International Living Future Institute that evaluates a company’s social justice and equity practices. Slocum claims 3form is the first manufacturing company to earn the certification.
“For 3form, this label reinforces our commitment to ethical labor practices, diversity and environmental stewardship, holding us accountable for maintaining high standards across these areas,” she says. “Our commitment and transparency towards sustainability make us stand out.”
Get curated news on YOUR industry.
Enter your email to receive our newsletters.
Latest from Recycling Today
- Dow, Mura Technology cancel chemical recycling plant in Germany
- Brightmark, Lewis Salvage partnership processes 1M pounds of medical plastics
- US paper recycling rate, exports down in '24
- Century Aluminum to restart idled production at South Carolina smelter
- Teaching kids the value of recycling
- ELV Select Equipment, Reworld aid NYPD in secure firearm disposal
- Some observers fear plastics treaty talks veering off course
- Advanced Polymer Recycling acquires TKO Polymers