The industrial shredder has grown to play a huge part in the recycling and waste industries. These machines are used in applications that range from reducing the size of material prior to processing to serving as a secondary device prior to manufacturing a finished product in the WTE (waste-to-energy) or RDF (refuse-derived fuel) sectors.
Regardless of application or industry, shredders now are a key component in facilities throughout the world and must be maintained properly to keep an operation running efficiently and profitably.
Shredders are similar to balers in recycling operations in that they are typically large, fixed pieces of equipment. When a shredder goes down, the entire plant is down. Therefore, unplanned downtime can lead to significant expenses affecting the overall health of an operation.
Typically, shredder downtime is caused by either a lack of preventive maintenance (PM) or a lack of planned downtime for major maintenance that has been delayed. Usually these delays arise from an operation feeling it cannot afford to halt production to perform the required maintenance or repairs or because it lacks a program to manage the maintenance of the shredder.
When an operation has not established a PM program or puts off PM until a more convenient time, it will spend more time and money in the long run when the shredding system goes down unexpectedly.
Keys to success
When developing, managing and implementing an efficient PM program for shredding equipment, operations should consider the following:
- Does the company’s culture promote PM, allowing for hiring the proper personnel, establishing adequate spare parts inventories and scheduling time for PM?
- Does the operation have qualified and capable staff (mechanics and/or technicians) to carry out routine maintenance on the shredder?
- Are the employees who are assigned to operate and maintain the shredder trained properly as to how the original equipment manufacturer (OEM) intends the machine to be operated and maintained?
- How committed is the operation to executing a PM plan?
When a shredder goes down unexpectedly, one should consider whether the mechanic tends to trace the failure back to a lack of maintenance. That could be an indication that the operation does not have a culture that supports a PM program. The right employees may not be working on the machine at the right times, or the operation may not maintain a small parts inventory that prevents higher expenses in the future.
When it comes to common maintenance issues, service and/or parts managers for shredder manufacturers often say the company operating the machine does not have adequately trained personnel to perform proper maintenance, even if it has a PM program in place. The next most common answer is that the machine and the application are mismatched, i.e., an operation is using a wood grinder to shred paper in a document destruction operation or a unit designed for paper shredding is being used to process plastics.
Begin at beginning
The best advice I can offer is to build a PM program based on what the OEM recommends for the shredder and application.
Next, one should ask the manufacturer which companies (not direct competitors, of course) are operating similar machines in similar environments, so the operations can share information and tips about wear, parts, applications, etc.
A PM program should include these fundamental measures:
- Document daily inspections and include space for the operator to make notes for the maintenance department if action is required. Daily documentation is a must, allowing an operation to track maintenance issues and providing operator accountability.
- Document weekly inspections and maintenance by both operators and the maintenance department.
- Document monthly, quarterly, semiannual and annual inspections, tying in what the OEM recommends for the specific shredder and application.
Having a basic inventory of spare parts also is important. Operations should be sure to incorporate the recommended spare parts from the shredder’s manufacturer. Additionally, operations may want to investigate which spare parts industry peers find they need.
Plan for major maintenance events by anticipating which parts will be required and ordering them well in advance. Most OEMs will make arrangements for a price reduction or payment plan based on usage and quantities ordered. The key is for the operator to track wear parts use and to plan for their replacement.
Fluid analysis
To achieve optimal production rates, most shredders require regular maintenance of gear lubricants, greases and hydraulic oil. Fluids in particular are very sensitive to contamination, and even the smallest particle can create a problem.
When it comes to fluids, operations must be sure to note the condition of the fluids at the time of purchase. Not all fluids are filtered to the same level. Operations should ask their suppliers about the degree of the fluid’s filtration before purchasing replacement fluid so that it meets the shredder’s requirements.
Operations also should store fluids in a clean and dry environment that is kept at a moderate temperature and should test fluids as part of their PM programs.
Companies can use these basic guidelines for maintaining the fluids commonly used in a shredder:
- Gear oil – Visually inspect the oil in the shredder gear daily for contaminants and to ensure it is at the proper level. At 2,000 hours, sample the oil and replace if required. Replace the oil in the shredder’s planetary gear box at 1,000 hours.
- Hydraulic oil – Visually inspect this oil daily for contamination and to ensure it is at the proper level. Sample the oil every 1,000 hours. If adding oil, be sure to use the proper micron in the filter.
- Oil cooler – Inspect weekly, cleaning it to maintain temperature ranges.
- Oil filters – Visually inspect daily to check for seepage or leaks. Replace every 250 hours, though heavier usage may require more frequent changes.
- Grease – Add grease daily based on OEM recommendations. In addition, Zerks should be cleaned prior to adding grease.
Know your limitations
Two very good questions that I touched on earlier play a key role in the life of a shredder: Is the shredder the right machine for the application? Are the company’s employees properly trained in the operation and maintenance of the shredder?
Furthermore, if the shredder requires routine hard facing, is the operation’s mechanic or maintenance technician properly trained on how to perform this work?
Additionally, if a company is hard facing more often than the OEM recommends, it may indicate the shredder is wrong for the application.
Regardless of the application and shredder type, it is vital to properly maintain the machine to maximize the overall efficiencies in operations and ultimately the profitability of the plant.
The author is with Midwest Recycling Service and Sales (MRSS), Cartersville, Georgia, and can be contacted at robb@mrssinc.com.
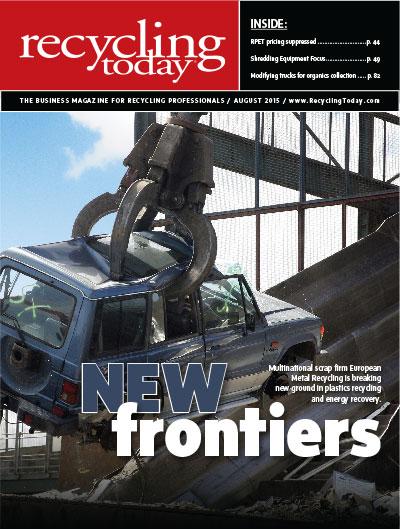
Explore the August 2015 Issue
Check out more from this issue and find your next story to read.
Latest from Recycling Today
- Corrugated market continues to recover from hurricane damage
- Nexans to make recycled-content copper
- Nucor sees slimmer Q3 profits
- Analysis: Plastic recyclers confront complications
- Mercedes-Benz opens battery recycling plant in Germany
- Sage Sustainable Electronics acquires Relectro
- TerraCycle acquires North Coast Services
- Liebherr holds US training event