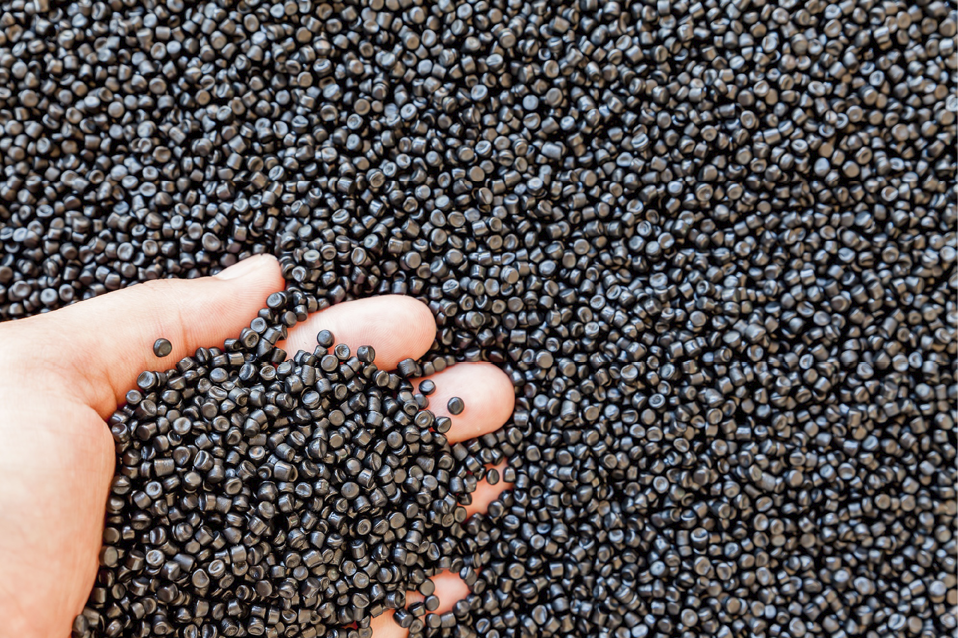
1. How would you describe the state of plastics recycling in North America?

Van Dyk Recycling Solutions
Head of Business
Development, Plastics
Plastics recycling is evolving but still faces major challenges as material types are more varied and complex than ever. This complexity often creates issues in sorting, making it difficult for converters to work with. While there has been progress in recovery of polyethylene terephthalate and high-density polyethylene, other materials like film, flexible packaging and mixed plastics are harder to isolate cleanly.
The good news is we are seeing more investment in plastic recovery facilities, or PRFs, that are designed specifically to meet the demands of today’s plastic streams. While collaboration across the entire value chain has improved, more of this type of collaboration is needed to close the gap.
2. How do you see plastics recycling evolving in 10 years?
We are entering an era where plastics will be sorted with more precision thanks to a combination of artificial intelligence- (AI-) driven equipment and automation. Demand for higher-purity bales from reclaimers and chemical recyclers will continue to rise, and facilities that can deliver consistent, high-quality feedstock will be well-positioned.
We also expect more regulatory pressure, from extended producer responsibility legislation to recycled content mandates, which will drive innovation and accelerate the adoption of advanced sorting technologies. All of this starts with consistent, reliable market demand backed up by long-term end user contracts.
3. What is the biggest issue plastic recyclers face?
Feedstock inconsistency and reliable end markets are the biggest hurdles. From one load to the next, composition and contamination can vary dramatically. That unpredictability puts pressure on recovery rates, throughput and bale quality.
To stay competitive, PRFs need highly adaptive systems—configurations that can react in real time to different material blends and contamination. Optical sorting, proper dosing and material flow control are essential. The use and advancement of AI is allowing systems to be able to audit in line and adjust processing parameters quickly without much human or manual intervention.
4. How is advanced or chemical recycling affecting the current landscape?
Chemical recycling is creating demand for materials that previously were considered residue. Reclaimers need a cleaner, better-sorted plastic input that mechanical systems like ours are uniquely equipped to supply. This has opened new markets, particularly for flexible packaging and mixed polyolefins. For PRF operators, it means designing a system that not only can produce high-quality bales but also generate clean streams for advanced recycling partners. It’s not about one method replacing another, it’s about synergy.
5. How important is equipment selection or sequencing when designing/building a PRF?
It’s everything. A successful PRF is more than just a collection of optical sorters—it’s a fully integrated system where every component plays a role in maximizing purity and recovery. From presizing to conveying to the sequencing of optical units, layout and flow determine how well the system performs.
At Van Dyk, we emphasize proper dosing, consistent material spread and the right number of detection points. Thoughtful sequencing leads to cleaner output, higher throughput and better margins.
Get curated news on YOUR industry.
Enter your email to receive our newsletters.

Explore the July 2025 Issue
Check out more from this issue and find your next story to read.
Latest from Recycling Today
- Deloupe offers trailers for the recycled metals market
- Greenwave to undertake another reverse stock split
- CAI Custom Alloys acquired by EverMetal
- Cronimet finalizes JV with battery materials firm
- Producer registration opens for California’s packaging EPR program
- Nexus Circular adds former Braskem America CEO to board of directors
- Houston receives new recycling trucks
- Ace Green unveils system to support antimony recovery, lead battery recycling