It has been well documented that newsprint production is declining steadily in much of the developed world. The situation is undeniably difficult for newsprint producers, who are closing capacity to better align with demand. Paper stock companies that base a large part of their business on the supply of old newspapers (ONP) also are challenged by the situation, as they are confronted with declining generation.
No news fit to print
According to the Montreal-based Pulp and Paper Products Council, an association of paper and forest products companies, North American newsprint production has fallen from a high-water mark of 15.79 million metric tons in 1990 to 6.44 million metric tons in 2013, a 59 percent decline in the past 13 years.
As considerable as that decline is, a further decline may yet occur. Derek Mahlburg, an economist with the forest products research group RISI, based in Boston, says he expects to see further erosion in newsprint production. “North American newsprint production will continue to be challenged by persistently heavy declines in the domestic market and further (newsprint) capacity reductions,” he says.
The offshore market has been a source of optimism for the North American newsprint industry over the past several years. “In 2013, export gains offset about 44 percent of the loss in domestic tonnage,” Mahlburg says, “but we believe that offshore markets are becoming saturated, which will make it difficult for the North American industry to continue to find export growth.”
Mahlburg says North American newsprint exports are well off their 2008 and 2010 levels as global demand declines, “even excluding mature markets like North America, Western Europe, Japan and China.”
While North American newsprint exports grew substantially in 2013, the growth could be attributed primarily to regaining market share from European producers, who removed 850,000 metric tons of capacity last year, he says. “As a result, we don’t expect these gains to be repeated in 2014, especially since Russia and China have been increasingly active in international newsprint markets over the past several months,” Mahlburg adds.
Yesterday's news
The downward spiral in newsprint consumption has resulted in a slew of newsprint machines closing throughout North America (as well as throughout Western Europe). Paper companies that have traditionally produced newsprint are shifting some of their production from groundwood newsprint to other types of paper products, such as packaging grades. SP Fiber Technologies, formerly SP Newsprint, has converted or is in the process of converting two of its newsprint machines—one in Dublin, Ga., and the other in Newberg, Ore.—from newsprint to packaging paper.
Other paper companies are looking at similar strategies, moving from producing what is perceived to be a steadily dying grade—newsprint—to packaging paper, a grade that is considered to have the potential for dynamic growth.
The paper company Packaging Corp. of America (PCA), Lake Forest, Ill., which recently acquired Boise, is considering converting an idled newsprint machine at the Boise DeRidder, La., plant from newsprint to packaging paper.
Wilmington, N.C.-based Atlantic Packaging Products also converted its idled Whitby, Ontario, newsprint mill to produce 100-percent-recycled lightweight paper.
However, Mahlburg says such conversions “haven’t always been straightforward to implement successfully in the past, which may limit the amount of machines that are able to explore this avenue.”
International edition
The extended slump in newsprint markets has left the handful of large newsprint producers unsteady at best. For instance, Montreal-based Resolute, the largest newsprint producer in North America, turning out roughly 39 percent of the continent’s newsprint, continues to shutter capacity as it tries to balance supply with demand.
Of course, declining newsprint production means declining generation of ONP. According to a source, Resolute is using more coated paper and less groundwood paper in its raw material for its mills as a result of the decline in ONP generation.
During Resolute’s recent webcast to discuss its 2013 financial performance, the company noted that North American newsprint demand declined by 9 percent in 2013, with demand from newspaper publishers down by 10 percent and demand from other end users down by 6 percent.
The challenges in newsprint markets also are being felt by producers of the grade in Europe. Norske Skog, headquartered in Oslo, Norway, recently released a report noting that large capacity cuts in newsprint and uncoated magazine paper production have led to improved market balance for the two grades.
Despite this balance, Norske Skog says markets remain weak. The company points out that demand for newsprint in Europe declined by 6 percent in 2013 from the prior year.
Similar to the approach taken by some North American mills, Norske Skog also is converting one of its newsprint machines to produce coated magazine paper at one of its paper mills in Australia.
Seen & heard
Despite the decline in newsprint production and the conversion of some machines from newsprint to packaging grades, ONP is still in demand as a raw material. However, there are challenges associated with obtaining this grade.
In addition to Resolute, SP Fiber Technologies says it has found growing obstacles to obtaining the clean ONP it needs to make recycled-content newsprint. During a session that addressed the challenges associated with ONP markets at the Paper Recycling Conference & Trade Show, hosted by the Recycling Today Media Group in October 2013, Bev Timmins, director of procurement for SP Fiber Technologies and SP Recycling, said, “The degradation of the grade is costing us lots of money and making it hard to make finished product.”
Hannah Zhao, who specializes in recovered fiber for RISI, says she sees limited upside for ONP.
“I don’t think there is a good solution to these problems. Declining quality and supply are the trends that no one can reverse,” Zhao says. “So consumers may have to face it by securing their own supply (at a relatively higher cost but better quality).”
Zhao adds, “They may be able to increase the prices for their finished products to cover the increase of their cost. If not, they may have to switch to other paper grades or shut the machines.”
With less ONP being collected through residential recycling programs, many processors are developing strategies designed to make up the difference.
To offset the decline in ONP supply, some material recovery facility (MRF) operators are blending ONP with mixed paper to create a “soft” mixed paper grade. Several processors say that because the price differential between mixed paper and ONP is so narrow (less than $15 per ton), it doesn’t make economic sense to separate ONP to be sold as a stand-alone grade.
“It is hard for MRFs to justify pulling out the wet strength, carrier stock and other materials to make No. 8 news when we are only getting a few bucks more,” another producer of ONP says.
This move to produce a soft mixed paper grade, several paper stock dealers say, has resulted in the disappearance of No. 7 ONP and in the labeling of No. 8 deinked news as No. 6 news.
The blending of these grades may be a challenge for consumers who rely on groundwood paper as a raw material, but other companies have welcomed the change. A number of recyclers in the eastern half of the country say Pratt Industries, based in Conyers, Ga., operates a number of recycled paperboard mills that can use a mixed paper grade that includes a fair amount of ONP.
While Resolute operates its Paper Retriever bin program in approximately one dozen states, through which it has been able to secure a steady supply of fairly clean ONP, another source says the company is using more coated grades and less groundwood paper in its raw material mix.
One ONP consuming sector that has been less able to adapt to these changes in ONP generation and recovery is cellulose fiber insulation producers.
Beth Royse, the head of purchasing for GreenFiber, Charlotte, N.C., a manufacturer of cellulose fiber insulation, fire and sound products made with a minimum of 85 percent paper fibers, says she is challenged by the lack of supply and by the quality concerns associated with ONP. “My intake used to be all ONP, but now it is around 50 percent ONP,” she says.
Because GreenFiber does not run material through a pulper, it needs to be clean and dry. To compensate, Royse says GreenFiber has sought out other types of groundwood paper, including telephone directories.
However, she says she often must go “into the weeds” to find the material quality she needs to for GreenFiber.
As for the possibility of pulling cleaner ONP from single-stream collection programs, Royse says that once the ONP is commingled with other materials, it can’t be brought back to its original quality. “You will have to find a new source or pay to clean it up,” she adds.
Not all paper stock dealers are bearish on the long-term future of ONP, however. Leonard Zeid with the paper recycling firm Midland Davis, St. Louis, says ONP is still readily available. He says more municipalities are introducing curbside collection programs and, while less ONP is being generated, the growing number of residences that are recycling at the curbside has more than offset the decline in per-person newsprint usage.
The author is senior editor of Recycling Today and can be contacted by emailing dsandoval@gie.net.
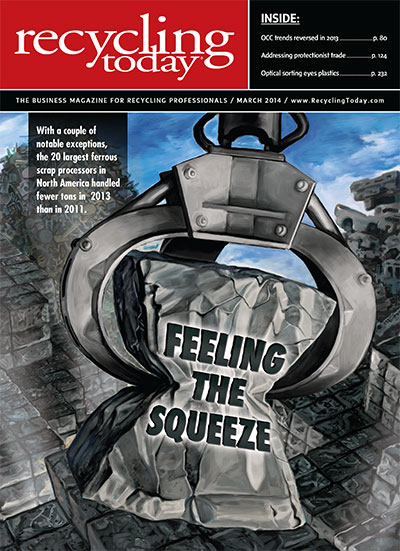
Explore the March 2014 Issue
Check out more from this issue and find you next story to read.
Latest from Recycling Today
- Bridgestone introduces retreating plant virtual tour
- USTMA announces Tire Recycling Foundation
- Dow announces agreement with Freepoint and MOU for Asia Pacific market with SCGC
- Mixed signals chracterize ferrous market
- Researchers look into ironing out a secondary aluminum limitation
- Analysis: Chemical recycling’s ‘inflection point’ nearing
- Machinex system in Québec targets organics diversion
- Northern Shenandoah region awarded $3.9M for recycling infrastructure