Indeco North America adds two locations to dealer network
Indeco North America has added two new dealers, Gibson Machinery LLC and W.I. Clark Co., to its distribution network. The Milford, Connecticut-based company provides hydraulic breakers, compactors, steel shears, crushers, grabs and pedestal booms for demolition, mining, recycling and road construction applications.

Founded in 2003, Gibson Machinery sells, services and supports construction equipment throughout Ohio, Pennsylvania and West Virginia. It has two locations in Oakdale, Pennsylvania, and in Cleveland.
W.I. Clark, established in 1925, sells, services and supports construction equipment throughout Connecticut. It has three locations in that state: Danbury, Plainfield and Wallingford.
“Indeco is pleased to partner with W.I. Clark and Gibson Machinery,” Bill Pankracij, Indeco North America public relations analyst, says. “As dealers with many years of experience in the industry and exceptional insight into their respective markets, they will be a great addition to the Indeco North America dealer network.”
More information on Indeco is available at www.indeco-breakers.com.
SWANA recognizes two MRFs designed by BHS
Eugene, Oregon-based Bulk Handling Systems (BHS) has announced that its customers are recipients of 2017 Excellence Awards for recycling systems from the Silver Spring, Maryland-based Solid Waste Association of North America (SWANA).
GreenWaste Recovery’s single-stream material recovery facility (MRF) in San Jose, California, was named the Gold Award recipient by SWANA. The Silver Award went to Emerald Coast Utilities Authority (ECUA) for its 25-ton-per-hour (tph) single-stream MRF in Pensacola, Florida. Both MRFs use systems designed, manufactured and installed by BHS.

Increased demand to process commercial and residential single-stream products with greater purity requirements prompted GreenWaste to add its newest recycling system, BHS says. Designed to process 35 tph, the plant averaged more than 50 tph in 2017 with what BHS calls “exceptional process uptime.”
This is the second SWANA Gold Award for GreenWaste, having previously won in 2008 for the company’s 40-tph mixed waste MRF, also built by BHS. The company has hired BHS to provide a major overhaul of that facility in 2018.
ECUA partnered with Escambia County to go from planning to completion of the $10.7 million project in 18 months. The undertaking included construction of a 53,460-square-foot building and a single-stream recycling system.
ECUA says the MRF is performing at a high level and exceeding financial targets.
“We’re proud that our systems are exceeding expectations and providing positive financial results for our customers,” BHS CEO Steve Miller says. “GreenWaste and the ECUA are organizations that offer exemplary recycling programs, and it’s exciting for us to see them awarded for excellence by their peers.”
Visit www.bulkhandlingsystems.com for more information on BHS equipment.
Eriez touts the success of its Shred1 ballistic separators
Since it released the Shred1 ballistic separator six years ago, Eriez, Erie, Pennsylvania, says it has installed units in various shredding yards, steel mills and slag processing facilities throughout North America. These separators use ballistics to upgrade frag by segregating the copper-bearing materials from the rest of the ferrous materials. Customers using Shred1 units report increased revenue and reduced overhead, the company says.
Shred1 Separators deliver a premium low-copper ferrous product and a traditional No. 2 shred. The low copper material, or No. 1 shred, is about 75 percent of the total volume, Eriez says. It goes to a stacking conveyor without going through a picking conveyor and is typically 0.16 to 0.17 percent copper.

“This No. 1 shred fraction has proven to be very desirable to steel mills,” says Eriez’s Chris Ramsdell.
The No. 2 fraction, high in copper, is the other 25 percent of the total material, according to Eriez. It goes through a manual picking station to recover copper-bearing material.
“We have customers that used to manually pick 7 pounds per ton of ferrous processed,” Ramsdell says. “After installing the Shred1, the pickings went to 13 pounds per ton. This is being accomplished with reduced picking labor because they only need to pick through 25 percent of the ferrous stream. Pickers are more efficient because of reduced volume.”
Eriez has made some minor modifications to the design of Shred1 since its 2011 introduction.“A couple of years ago, we added a third pulley that directs the frag down and away from the underside of the machine and into the No. 1 shred chute,” Ramsdell says. “We also redesigned access panels and bearing covers to allow for greater maintenance accessibility.”
More information is available at www.eriez.com.
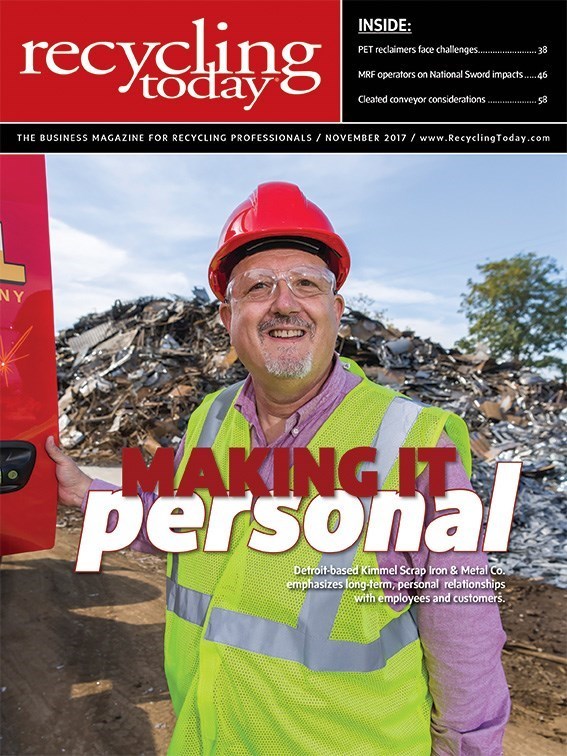
Explore the November 2017 Issue
Check out more from this issue and find you next story to read.
Latest from Recycling Today
- Bridgestone introduces retreating plant virtual tour
- USTMA announces Tire Recycling Foundation
- Dow announces agreement with Freepoint and MOU for Asia Pacific market with SCGC
- Mixed signals chracterize ferrous market
- Researchers look into ironing out a secondary aluminum limitation
- Analysis: Chemical recycling’s ‘inflection point’ nearing
- Machinex system in Québec targets organics diversion
- Northern Shenandoah region awarded $3.9M for recycling infrastructure